FEATURE
Investigation of Additives for MDI-based Composite and Binder Applications
Investigation of Additives for MDI-based Composite and Binder Applications
By Jason H. Stengel, Momentive Performance Materials Inc., Friendly, West Virginia
Part one of an article about the use of pMDI-based binder additive technology in wood composites, presented at the 2023 Polyurethanes Technical Conference.
Polyphenylene polymethylene polyisocyanate (pMDI) has been widely used as a binder in the commercial production of wood composites such as oriented strand board (OSB). pMDI provides various physical and mechanical properties to the composite material and enhances its processability. Improved processability may include, for example, shorter pressing cycle times, which result in increased productivity.
These types of composite panels may be manufactured by introducing the binder, such as pMDI, into a rotary blender that contains wood particles. After the binder and the particles have been mixed, the mixture can be introduced into a mold or a press where it is subjected to heat and pressure to form the composite panel. One drawback with the pressing process, however, is that the press times can be long and high temperatures are typically required. Press time and temperature can be reduced using additives. However, with and without the use of additives, there are opportunities throughout the process for pre-cure to occur, which could negatively impact processing and performance of the resulting panels. The present technology attempts to address one or more of these issues.
This paper will disclose Momentive Performance Material’s recent developments in pMDI-based binder additive technology. These developments are focused on improving processing and performance of wood composite products produced through the use of MDI-based binders. Data will be presented showing improvements in processing and physical and mechanical properties through the use of additives. Processing experiments include the ability to reduce pMDI use level, reduction in press time, and reduction in press temperature. Key performance criteria investigated are moisture properties, bond strength, and flexural properties. OSB grades have set minimum specifications; thus, using these additives, the criteria for such grades may be met with reduction in the use level of binder resin as well as reductions in energy cost by lower temperature and time in the pressing process.
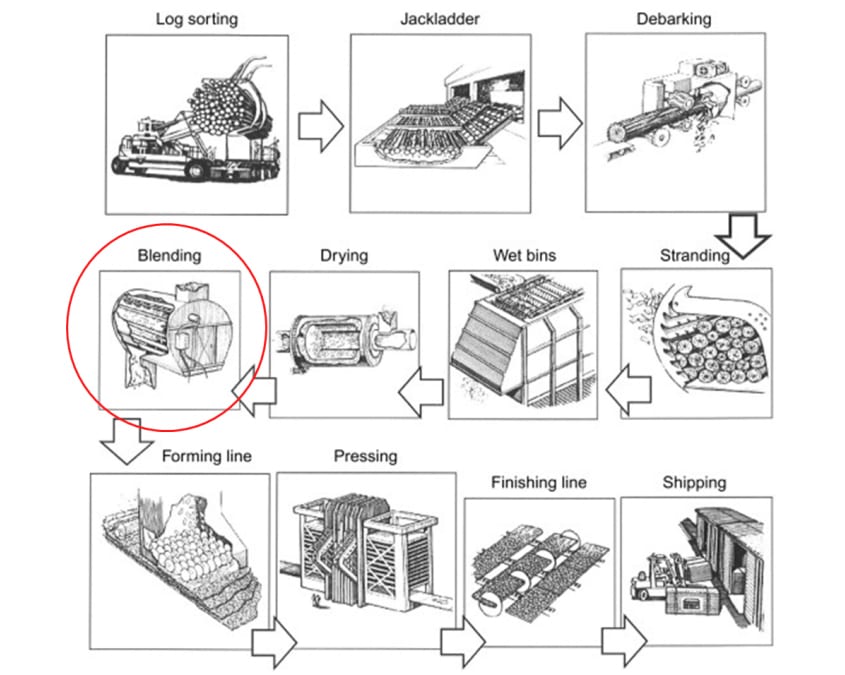
Figure 1. General process overview of OSB production (5).
Introduction
Composite and engineered wood products are frequently used materials for construction and other purposes due to several advantages, including performance, ease of use, and production, cost, and availability of raw materials. The wood industry is vast and versatile, like the PU industry, with a variety of processes utilized to obtain specific functioning materials from OSB and plywood to wood-plastic composites and many other construction materials (1). Engineered wood products are one of the most important raw materials critical to durable construction (2). There are several efforts to utilize sustainable materials, reduce, reuse, recycle, and provide enduring products for the consumer (3) (4). With these efforts in mind, Momentive is providing solutions to enable more efficient processing for a more sustainable world. In continuation of previously reported latent catalysis research, Momentive has identified an additive composition for use in MDI-binder applications; specifically oriented strand board (OSB).
The focus within this communication will be on the processing of OSB and potential improvements therein along with analysis of the performance of the produced panels and comparison to state-of-the-art resins. Momentive’s developments are geared toward process improvement potential and the resulting product’s physical/mechanical properties. This paper will look at the process for OSB production and identify areas where an additive may bring some advantages. In addition to the process improvements, the resulting product should provide equivalent or improved properties, which in turn may provide further benefits to the producer and consumer.
In the following pages, we will demonstrate the performance of new additives in providing benefit to the process of OSB production as well as improvements in the physical and mechanical properties. At high use level of additive (10 – 40% by weight based on resin charge) improvements in water absorption, internal bond strength, and flexural properties are noted. Testable panels1 were produced at reduced press time and temperature and with variable resin loadings ranging from 2.5–5%. A second study at reduced use level reinforced the findings from the first study; specifically, the water absorption and flexural properties with the use of UAX-1319.
Glossary and Terms
- Bin life can be defined as the time elapsed after resin has been applied to strands and prior to the strands being formed and pressed.
- Internal bond strength (IB) is a measure of the inner bond quality/strength between the strands of the panel. This property is determined via a tension force applied perpendicular to the panel surfaces. ASTM D1037, Section 11 provides details on this test.
- Water absorption testing is conducted via ASTM D1037, Section 23. This test provides methods for determining the mass and volume of water absorbed by a wood-base panel specimen of known initial moisture content (MC). Water Absorption (WA) is either recorded as mass or volume (typically both) and then reported as a percentage increase with respect to the initial MC in the specimen. Less water absorption is preferred.
- Thickness Swell (TS) is a measurement of the thickness of the panel edge or at a point one inch to the interior of the edge and is reported as a percentage increase versus the initial thickness of the panel specimen. Less swelling is preferred and indicates less water absorption.
- Moisture Content (MC) refers to the total amount of water in a piece of wood or wood-base composite and is defined as the weight of water in the wood divided by the weight of the wood. As part of this work, the MC was determined in accordance with ASTM D4442, Method A – Primary Oven-Drying Method.
- Flexural properties that were measured via procedures outlined in ASTM D1037, Section 9 include the following: Modulus of Elasticity (E) and Bending Stiffness (EI) – Panel bending stiffness is the capacity to resist deflection and is represented in bending equations as EI. The E is the apparent modulus of elasticity of the material and the I is the moment of inertia of the cross section. Traditionally in the OSB industry, the units of EI are lbf-in.2 per foot of panel width.
- Modulus of Rupture (MOR) and Maximum Moment (MM) – Bending strength capacity is the maximum moment (MM). The maximum moment of a bending specimen is calculated as the extreme fiber stress of the material (MOR) multiplied by the section modulus (S). Traditionally in the OSB industry, the units of MM are lbf-in. per foot of panel width.
- (APA Test Method) D4 Moisture Cycle is a quality control method to accelerate bond degradation commonly used in the OSB industry. The single cycle is comprised of subjecting wood-base panel specimens to a vacuum-pressure soak and redrying. The specimens are then tested dry according to the appropriate test method. In this case, D4-cycled specimens were tested in bending per ASTM D1037 in the same manner as noted for determination of dry flexural properties.
- Retained Flexural Strength is a ratio of the bending strength (MM) of the cycled (D4) and uncycled (control) specimens.
Background
OSB process and areas of potential improvement
Momentive’s catalyst and additive portfolio includes a variety of options to facilitate the production of polyurethane foams. Recent developments have been in delayed action, thermally activated, isocyanate stable materials. This paper is a report of these endeavors and the performance thereof in OSB production. The general process for OSB production is outlined in Figure 1, where the introduction of the additive could occur at the blending stage to provide processing benefit after the addition of isocyanate binder. The additive can be introduced at the blending stage as a part of the binder resin (pre-blended) or the additive may be introduced separately through the spinning disc atomizer, before or after the isocyanate is introduced.
One potential benefit of a delayed action thermally activated additive can be gained during the blending and stranding process. Strands are introduced to the blender following drying. If the strands are not permitted to cool prior to blending, the reaction may be initiated too early in the process due to elevated temperatures rendering the resin inactive. Ideally, the additive is not active, remaining dormant, and the resin does not react until the strands reach the pressing stage.
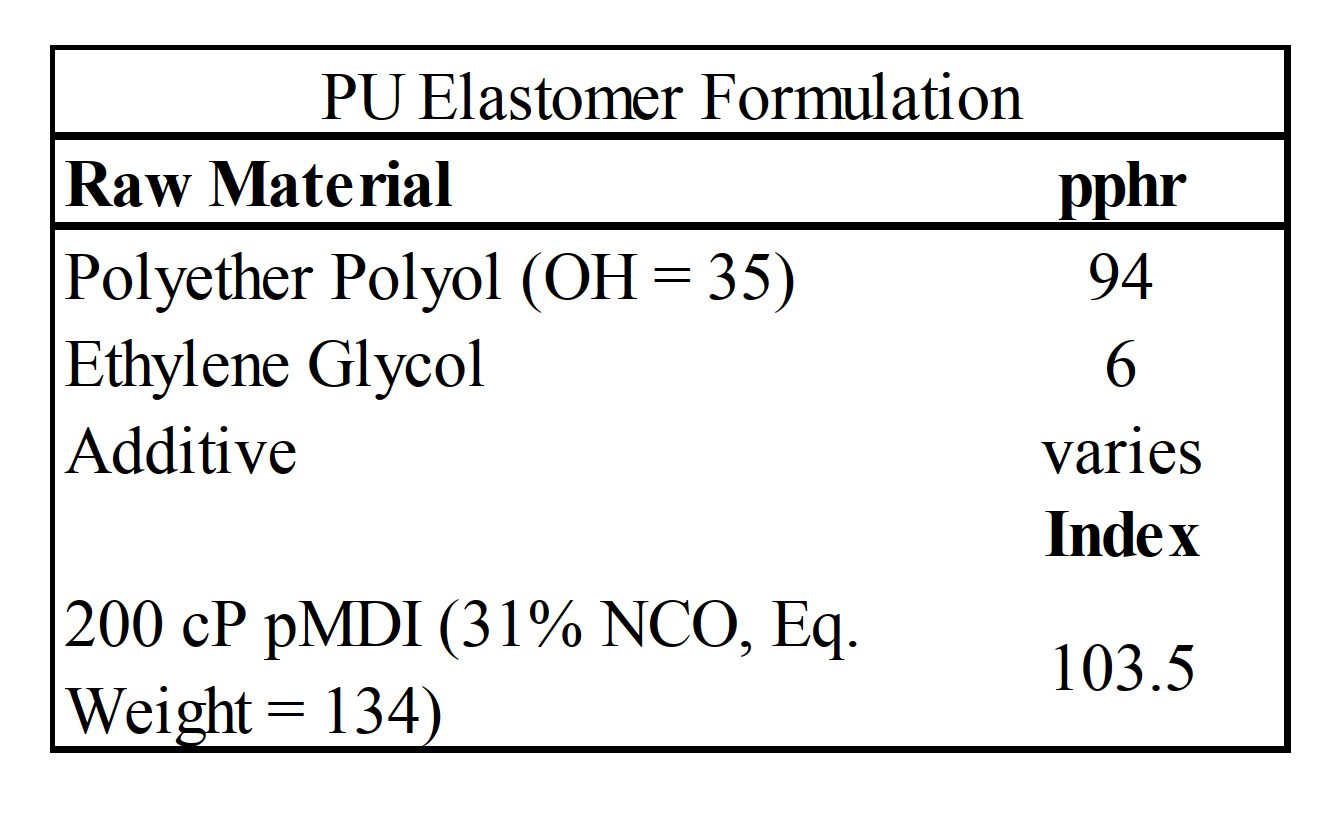
Table 1. Elastomer formulation. *Product formulations are included as illustrative examples only. Momentive makes no representation or warranty of any kind with respect to any such formulations, including, without limitation, concerning the efficacy or safety of any product manufactured using such formulation. **pphr = parts per hundred resin.
Pre-cure occurs when the reactive species are initiated prematurely and prior to reaching the press, which will inhibit their ability to provide adhesion to the layers of strands potentially causing the integrity of the produced panels to be poor. During the forming process, pre-cure could occur due to elevated/sustained temperatures as well as if there are slowdowns in the process. The latter may be an issue with the use of "fast-cure" resins, which activate at or near ambient temperatures.
Other potential advantages of an additive include improvement in processing through reduction in process press time and temperature to increase efficiency and reduced energy consumption. The bin-life of the strands following blending is a critical parameter as well, which can be defined as the time the strands are held (in a bin) after treatment with resin in the blender prior to forming and pressing. The requirement is that the resin will remain unreacted and active for use at the time of pressing. As the resin sits on the strands in open air, it may begin to react. Delaying this process as long as possible is critical to producing the desired grade panel. Typical processing conditions during the pressing process are elevated temperatures (415℉/212℃) for 1.5–4 minutes. Some of these topics will be addressed throughout this paper relative to the use of Momentive’s new developments and their impacts on process modification, panel integrity, and physical/mechanical properties of hand-formed OSB panels.2
Additive Screening
Initial testing to identify additive compositions with desired reactivity profiles in elastomer formulations (Table 1) were conducted via viscometry using a Brookfield® viscometer (Figure 2). UAX-1319 and UAX-1360 were identified as potential candidates early in the screening process. The comparative example in this case, DMDEE3, provided very quick reactivity in the elastomer formulation. The viscosity build in this system was targeted to be more delayed than that of DMDEE and this was achieved through the formulations of these three new compositions.
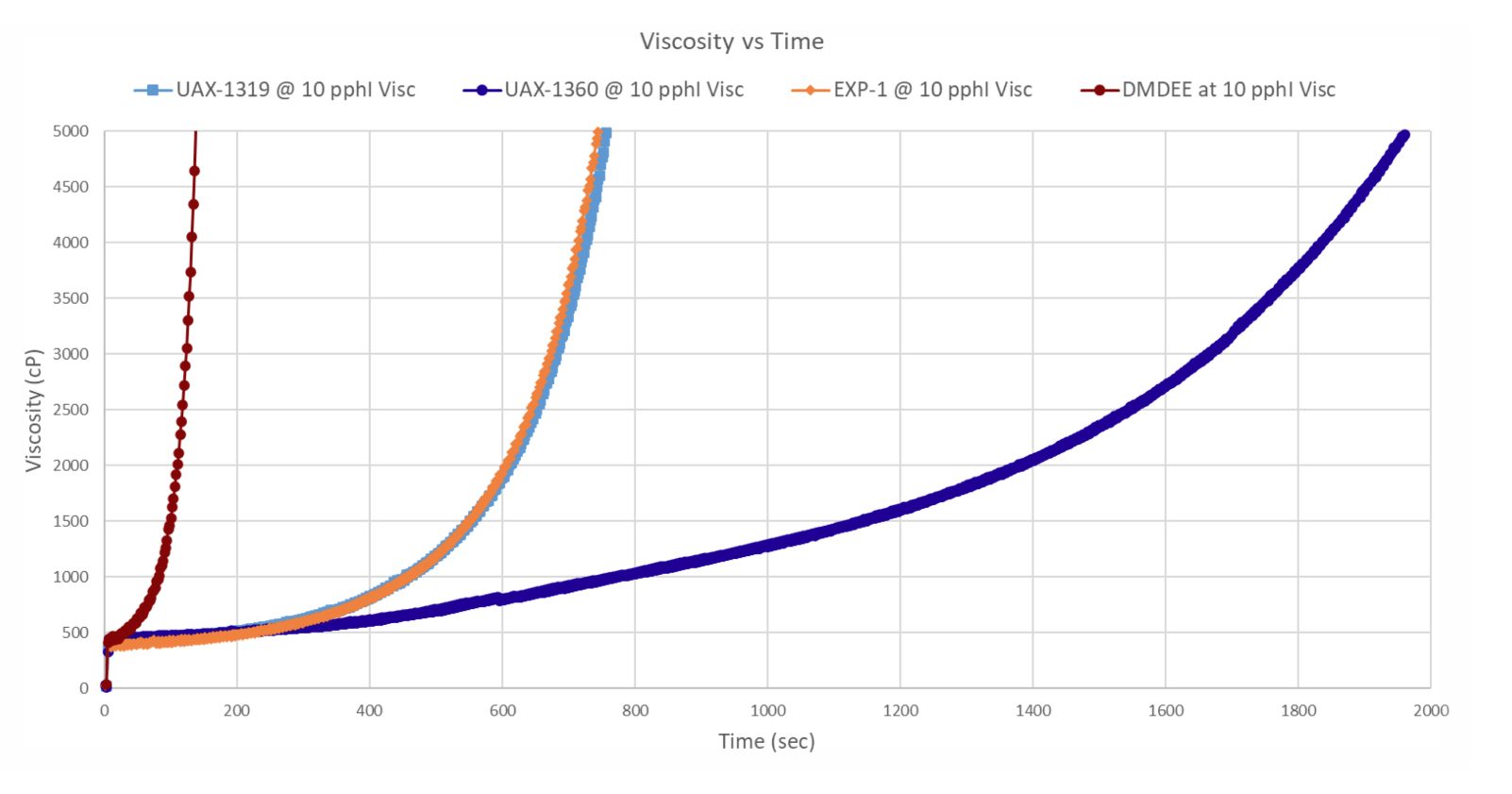
Figure 2. Viscosity build profile DMDEE vs. UAX-1319. **pphI = parts per hundred Isocyanate.
Once the potential compositions were identified, stability studies were conducted with high levels of the additive being charged to isocyanate followed by heating for extended periods to observe viscosity build (Table 2). The purpose of the additive is to facilitate reactivity of the isocyanate; therefore, some viscosity build is expected to occur particularly at elevated temperature. However, in the absence of pressure, water, and cellulose the viscosity build should not be excessive or too quick compared to isocyanate that does not contain additive.
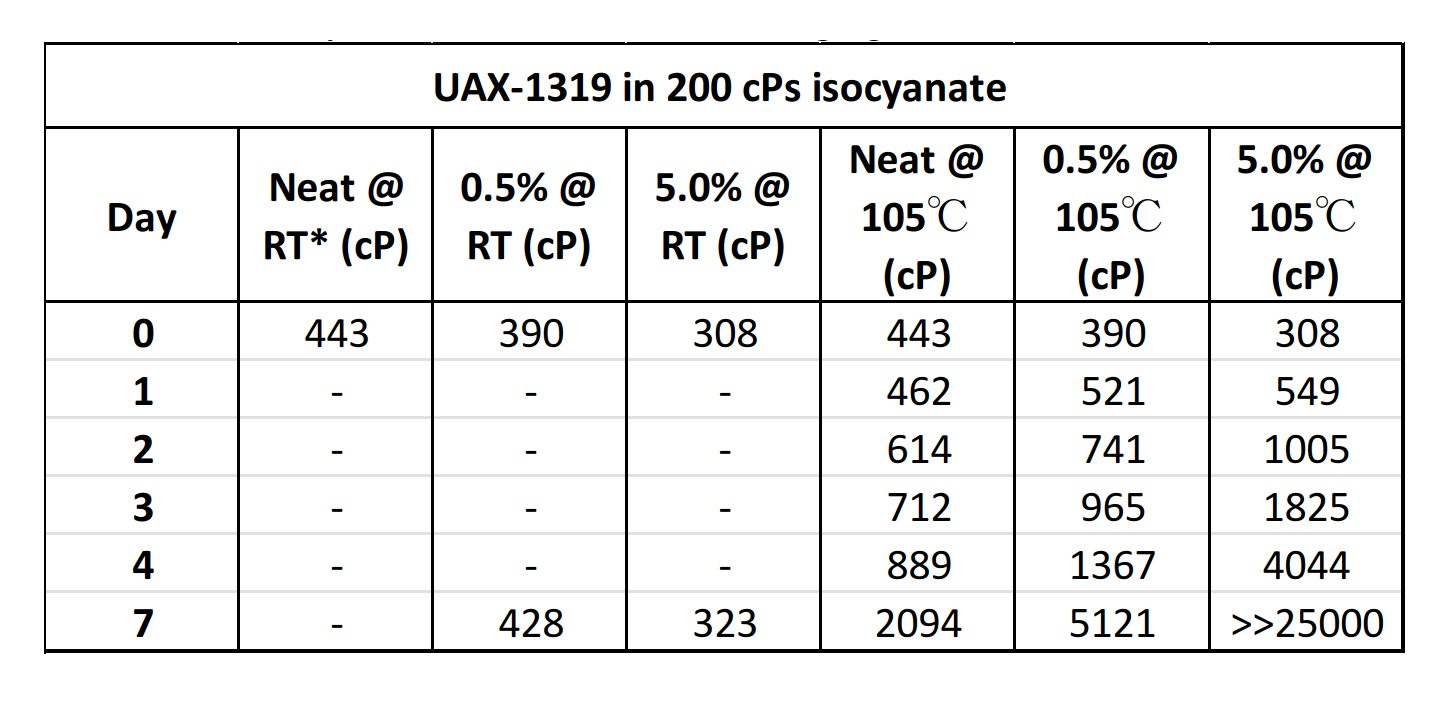
Table 2. Viscosity Measurement Accelerated Aging of UAX-1319. *RT = room temperature (ambient, 22-23℃) storage. All measurements were made at 20℃. - indicates no measurement made.
Table 2 shows the viscosity measurements of neat 200 cP isocyanate4 compared to samples of the same with UAX-1319 added at 0.5% b/w and 5.0% b/w isocyanate. After two days at 105℃, the viscosity build with the samples containing additive were just under three times that of the isocyanate without additive. The isocyanate without additive at ambient was approximately five times lower in viscosity than the heated sample after seven days. The sample containing 5.0% additive b/w isocyanate additive showed 10 times increase in viscosity after four days at 105℃. The sample loaded at 0.5% additive b/w remained liquid for up to seven days with a recorded viscosity of ~ 5121 cP. This study provided support for administering additive directly to the isocyanate if it would not be possible to third stream during the blending process.
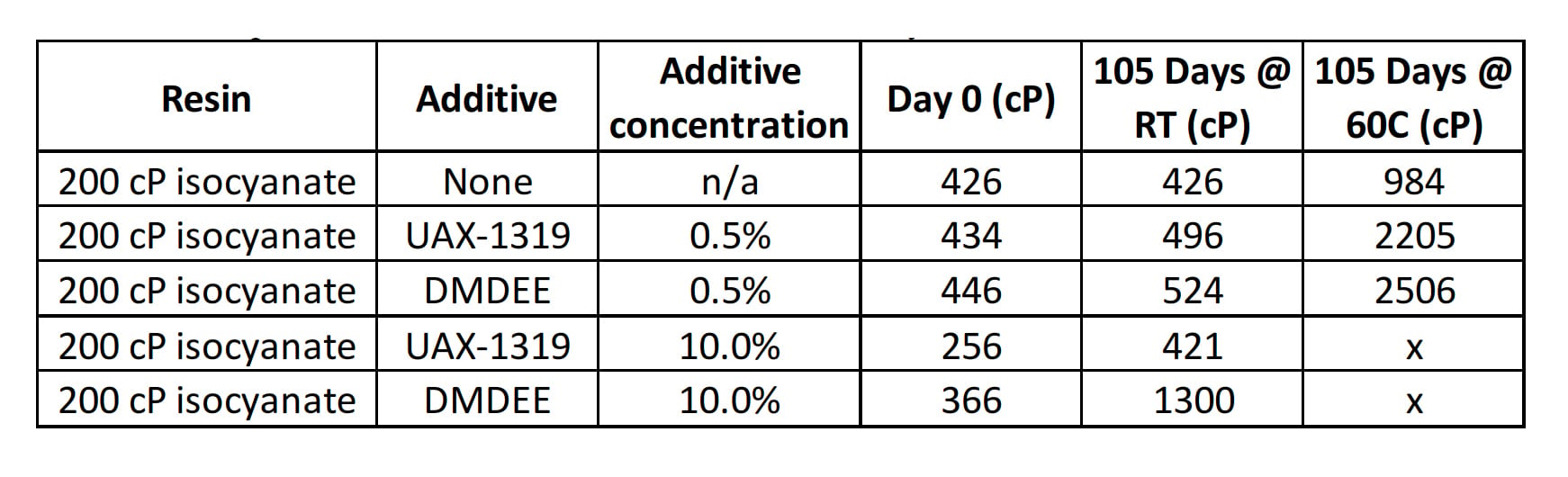
Table 3. Comparison of UAX-1319 to DMDEE – Stability at 60℃. *RT = room temperature (ambient, 22-23℃) storage. All measurements were made at 20℃. x indicates no measurement made.
The UAX-1319 was also compared to DMDEE (Table 3) in 200 cP isocyanate resin at 60℃ for an extended period where there is limited viscosity build for each at 0.5% use level and at the 10.0% use level. UAX-1319, in the absence of heat, provides no appreciable increase in viscosity. This would indicate that UAX-1319 would be acceptable in similar storage and processing to that of DMDEE relative to the isocyanate employed. The accelerated aging equivalent for seven days at 105℃ is 5.6 years and 105 days at 60℃ is equivalent to 3.7 years at 23℃ determined by using Eq. 1, derived from the Arrhenius equation.
Eq. 1: TimeAcc = TimeRT / Q10^(T1 – TRT) / 10
Where TimeAcc is the time at elevated temperature (T1) to achieve equivalency of TimeRT. TimeRT is the shelf-life (time at room temperature) typically based on weeks, months, or years. Q10 denotes the reaction rate for every 10℃ increase in temperature above storage temperature; typically two for most plastics. Thus, the reaction rate doubles for every 10℃ increase. T1 is the elevated temperature chosen (60℃ and 105℃ in this study) and TRT denotes the chosen ambient temperature at which the material will be stored (23℃ in this instance).
Through these experiments it was determined that it would be interesting to look at these compositions in a binder application utilizing pMDI resin. To this end, several new compositions were tested in the processing and performance of OSB panels5.
Experimental
Proof of Concept in Application
Two OSB panel studies were conducted. The initial proof of concept study was conducted to identify potential processing improvements as outlined above. Physical property analysis was also conducted with a focus on the water absorption prevention, internal bond strength, and Flexural Modulus of the panels produced. The first step, however, was to utilize the new materials successfully in the production of a panel. Further studies would be utilized to explore the initial findings relative to the processing and properties of the resulting panels.
Study 16:
Six different sets of experimental conditions were investigated. For each condition/experiment noted, one blend of strands was utilized to produce three panels. The data provided in the tables is an average of the specimens from each of the three panels.
- EXP# 1: Standard Conditions: 415°F press temperature with a press time of 180 seconds (20 seconds off gassing), 0.5% additive load if used, 0.75% wax loading, and 5% MDI load.
- EXP#2: Press time reduction of 20–40 seconds (10–20% reduction from 180 seconds).
- EXP#3: pMDI reduction (5% to 2.5%).
- Exp#4: Press time and pMDI loading — combination of reduced press time (EXP#2) and reduced pMDI loading (EXP#3).
- EXP#5: Press temperature was reduced to 300°F, increase by 25°F until under-cure subsided.
- Exp#6: Variable introduction of additive — either by pre-mix with resin or separate addition.
Study 27:
The second study utilized similar processing parameters focusing on the standard conditions of EXP#1 from the initial study. In this case six different conditions were utilized, centered around the standard process. For each condition/experiment noted three blends were prepared producing three panels each. The data for each parameter is an average obtained from the set of nine panels.
- Condition 1A: Standard conditions as noted with extended press cook time of 210 seconds (30 seconds longer).
- Condition 1B: Standard conditions repeated as noted above.
- Condition 3: Use of UAX-1319 in the standard process again at 0.5% use level relative to isocyanate mass.
- Condition 4: Use of UAX-1355 in the standard process at the reduced use level (0.5%).
- Condition 5: Use of UAX-1360 in the standard process at the reduced use level (0.5%).
- Condition 6: Use of fast-cure pMDI resin — same level as EXP#1.
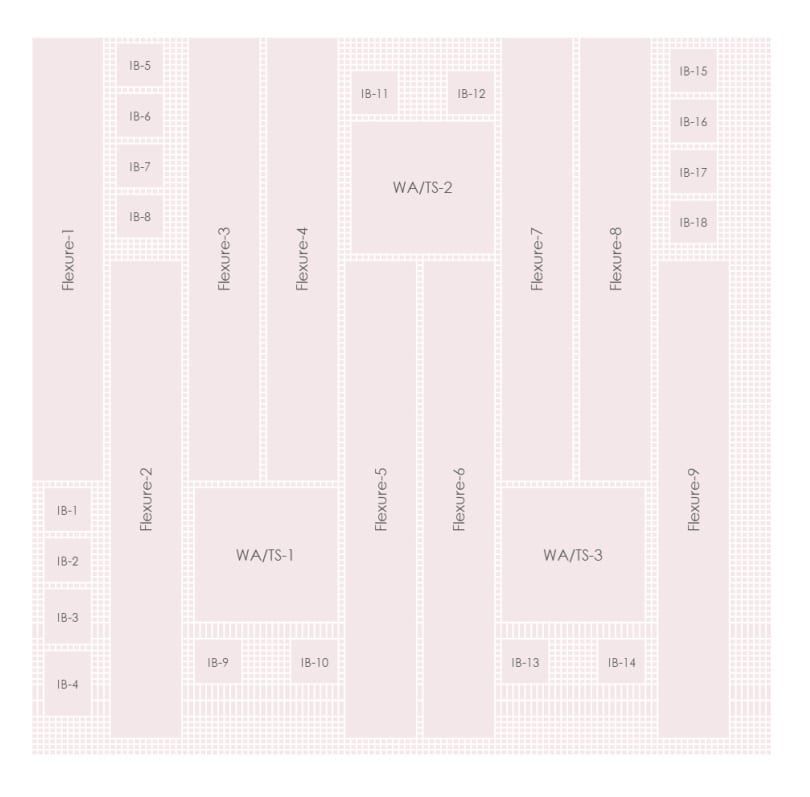
Figure 4. Cut Pattern #2, Study 2.10
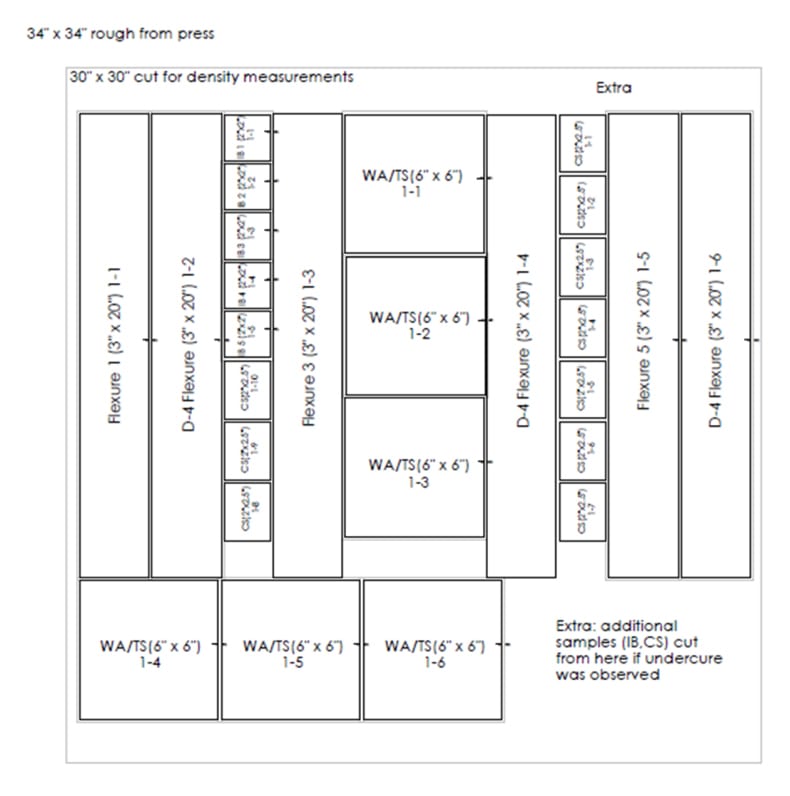
Figure 3. Cut Pattern #1, Study 1.9
Resin Blending, Stranding, and Pressing Process
Aspen wood strands were utilized for both studies. Typical wood type for this process is Aspen or yellow pine. Strands were received at ~5% moisture content and adjusted during blending to 8–10% moisture content. The strands were charged to the resin blender, followed by water to achieve the desired moisture content. Wax was then administered through the same atomizing apparatus (0.75% based on wood mass for all panels, both studies). Isocyanate was charged (5% based on weight of strands) via spinning disc atomizer (separate from the water/wax atomizer). The additive was then charged via atomizer (same as pMDI) at a level of 0.5%–1.0% based on wood mass8. Some experiments were conducted to gauge the performance difference of blending catalyst with isocyanate prior to adding to the blender. The strands were not dried prior to blending and were maintained at 70℉ (21℃/ambient).
One blend was prepared for each experimental condition to produce three panels per condition for triplicate analysis in study 1. Study 2 utilized three blends per condition, three panels per blend, for a total of nine panels per condition. Each blend was removed from the blender, weighed to appropriate mass to achieve a density of ~38 pcf, and then hand formed. The rough strands were placed in the press at 415℉ (212℃) for 180 seconds (20 second degas) under standard conditions. These variables were modified in various experiments.
The noted standard conditions were based on "normal" operating parameters at a typical mill. The variables investigated included the use of additive, additive level, pMDI level, press temperature, press time, and separate/mixed additive introduction. All blends were conducted in a 5'x10' blender with atomizer speed of 8700 rpm having two rows of holes at 0.180" diameter. Resin was introduced at 500 mL/min (5% loading), 300 mL/min (2.5% loading), and additive was introduced at 100 mL/min.
Four experimental materials UAX-1319, UAX-1342, UAX-1355, and UAX-1360 were the subject additives. UAX-1342, UAX-1355, and UAX-1360 are further developments based upon UAX-1319, with modified structures and compositions to attenuate performance. No use of additive was the control/comparative example in study 1; and in study 2, a non-additive experiment was repeated in addition to a "fast-cure" comparison experiment. DMDEE was utilized in a subset of experiments as a second comparative example in study 1.
After pressing, the panels were dressed (34"x34" rough from press) and cut to standard size 30"x30" targeting a thickness of 23/32" and a density of 38 pcf. Two separate cut patterns were used (Figures 3 and 4). The first set of data was obtained using cut-pattern #1 and the second study was similar with an increase in internal bond (IB) strength data points. Findings from the initial study, outlined in detail below, were that the new additives positively impacted the IB, water absorption/thickness swell (WA/TS), and flexural properties; specifically, the latter when subjected to the D4 moisture cycle. These findings prompted an emphasis on a larger number of data points for IB analysis to ensure statistical relevance for all data obtained.
Read part two of this paper, which presents the results and discussion, in the October issue of ASI. Learn more about Momentive Performance Materials Inc. at www.momentive.com/en-us.
Acknowledgements
The authors acknowledged Brandon Doss, technician, Momentive Performance Materials Inc., and the Advanced Structure and Composites Center at the University of Maine.
"Investigation of Additives for MDI-based Composite and Binder Applications" 2023 Polyurethanes Technical Conference 25-27 September 2023, San Antonio, TX, USA. Published with permission of CPI, Center for the Polyurethanes Industry, Washington, DC.
Endnotes
1. Testable panels were noted as not having any visual defects and the adhesion of the strands was complete without delamination.
2. Hand-formed panels are not oriented. Orientation impacts the bending properties.
3. 4,4’-(Oxydi-2,1-ethanediyl) dimorpholine (Dimorpholinodiethyl ether).
4. The isocyanate used in all experiments was a pMDI with 2.7 functionality, equivalent weight of 134, and viscosity avg. of 200 cP at 25℃ with viscosity growth rate of 10 cP/month.
5. Panels were produced and tested at the Advanced Structure and Composites Center at the University of Maine.
6. All experimental additives and DMDEE were charged based on wood mass in Study 1.
7. Experimental additives charged based on isocyanate mass.
8. These levels corresponded to a range of 10-40% additive based on MDI mass charged.
9. Provided by Advanced Structure and Composites Center at the University of Maine.
10. Provided by Advanced Structure and Composites Center at the University of Maine.
11. Conducted by Advanced Structure and Composites Center at the University of Maine.
12. Testable panels were noted as not having any visual defects and the adhesion of the strands was complete without delamination.
References
1. APA - The Engineered Wood Association. [Online] 2023. [Cited: April 15, 2023.] https://www.apawood.org/technical-research.
2. Kumar, Ranjana Yadav and Jitendra. Engineered Wood Products as a Sustainable Construction Material: A Review. [ed.] Meng Gong. Engineered Wood Products for Construction. s.l. : IntechOpen, 2022, 2.
3. Natural based polyurethane matrix composites reinforced with bamboo fiber waste for use as oriented starnd board. Mariana Dias Machado Lopes, Magno de Souza Padua, Juliana Peixoto Rufino Gazem de Carvalho, Noan Tonini Simonassi, Felipe Perisse Duarte Lopez, Henry A. Colorado, Carlos Mauricio Fontes Vieira. 2021, Journal of Materials Research and Technology, pp. 2317-2324.
4. Recent progresses in wood-plastic composites: Pre-processing treatments, manufacturing techniques, recyclability and eco-friendly assessment. Ammar H. Elsheikh, Hitesh Panchal, S. Shanmugan, T. Muthuramalingam, Ahmed. M. El-Kassas, B. Ramesh. s.l. : Cleaner Engineering and Technology, 2022, Vol. 8.
5. Nishimura, T. Chipboard, oriented strand board (OSB) and structural composite lumber. [ed.] Martin P. Ansell. Wood Composites. s.l. : Elsevier Ltd, 2015, 6, pp. 103-121.
6. National Institute of Standards and Technology and U.S. Department of Commerce. Performance Standard for Wood Structural Panels. s.l. : National Institute of Standards and Technology, 2019. PS 2-18.
Opening image courtesy of BanksPhotos / iStock / Getty Images Plus.