FEATURE
The Latest Market and Technology Trends in Solvent-free Lamination Adhesives
The Latest Market and Technology Trends in Solvent-free Lamination Adhesives
By Keith Potts, Technical Support Engineer at ChemPoint, and Kensen Hirohata, Marketing Manager at ChemPoint
Enhanced polyurethane solvent-free laminating adhesive systems facilitate the replacement of solvent-based adhesives, while addressing critical challenges of increasing usability.
The flexible packaging material market is expected to continue to grow significantly, due to the increase of the global population, resolution of food issues through food-waste reduction, and the economic growth of emerging countries. At the same time, social and environmental issues such as plastic waste and global warming need to be addressed. It is becoming more important for the entire industry to work to build a sustainable society through Corporate Social Responsibility (CSR) and other initiatives. To help curb global warming, the Japanese government announced its increased targets for realizing a sustainable society at the Climate Change Summit (COP26) in April 2021. Among the revised goals were reducing greenhouse gas emissions in Japan by 46% below the FY2013 level by FY2030 and the realization of a carbon neutral society in 2050. To realize these goals, it is necessary for industry, enterprise, and individuals to plan their actions using a backcasting approach and to implement these plans accordingly.
The Japanese lamination industry has been using solvent-based adhesives for years. Every year, the industry discharges hundreds of thousands of tons of carbon dioxide (CO2) and other greenhouse gases throughout the life cycles of its products, which include production, processing, and incineration. That said, Toyo-Morton estimates that CO2 emissions related to inks and laminating adhesives in packaging can be reduced up to 70% by substituting solvent-based products with solvent-free ones. As shown in Figure 1, the proliferation of water-based/solvent-free adhesives with low-associated CO2 emissions is more popular in countries such as the United States, Europe, and Southeast Asia (especially in the Philippines). Japan lags behind the world in terms of environmental responsiveness and needs to change its ways if it is to achieve a carbon-neutral society.
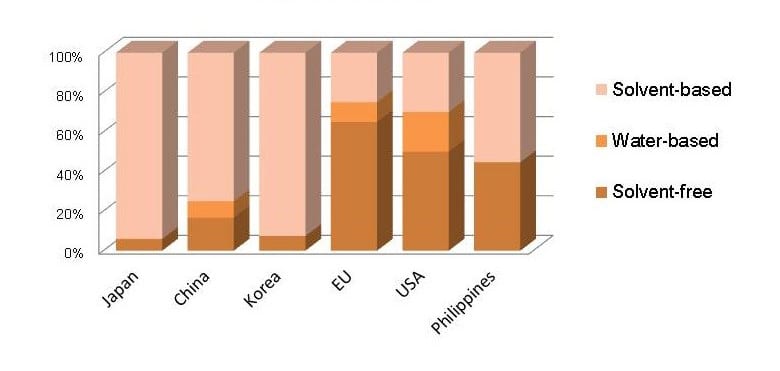
Figure 1. Market share of environmentally friendly adhesives (in-house research).
Addressing this issue, in line with the sustainability vision set by its parent company, the Toyo Ink Group of Japan, Toyo-Morton has set a target of increasing the proportion of solvent-free adhesives in its product mix in Japan to 30% by 2030 and 100% by 2050, and is promoting business and development activities accordingly.
High-Performance Solvent-Free Products
Currently, solvent-free lamination adhesives are mainly used for OPP/CPP, OPP/VMCPP, and PET/VMCPP packaging structures for snack foods. On the other hand, solvent-based adhesives are typically used for applications that require superior physical properties such as content resistance, heat resistance, and retort resistance, because they can form durable laminating structures. At Toyo-Morton, the company has enhanced its ECOAD™ series of polyurethane solvent-free laminating adhesive systems to facilitate the replacement of solvent-based adhesives, while addressing critical challenges of increasing usability and developing products for applications where the physical properties of the previous solvent-free adhesives had been insufficient (Figure 2).
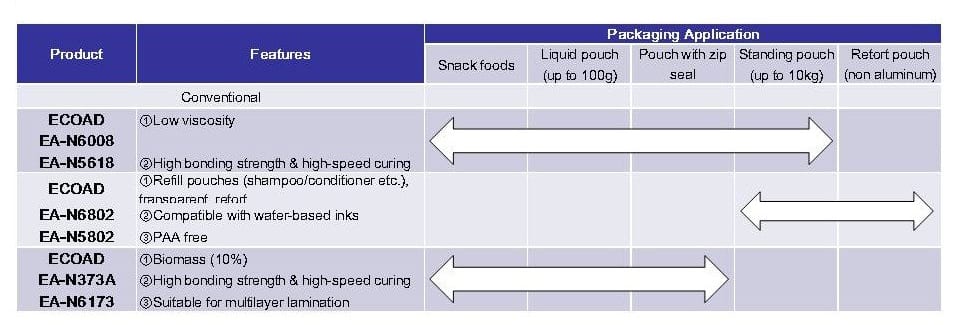
Figure 2. Application range of new ECOAD™ Series of solvent-free adhesives.
The company has developed three types of products: ECOAD EA-N6008/EA-N5618 solvent-free lamination adhesives for stand up refill pouches and resealable zipper bags, ECOAD EA-N6802/EA-N5802 adhesives for transparent retort pouches and water-based ink applications, and ECOAD EA-N373A/EA-N6173 adhesives made from biomass materials.
Solvent-Free Adhesive Systems for Stand-Up Refill Pouches and Zipper Bags
Traditionally, solvent-free adhesives were believed to be unsuitable for zipper bags and stand up pouches that must undergo demanding heat-sealing processes. In addition, packages with checkered patterns or designs featuring windows were considered difficult to laminate with solvent-free adhesives as they tended to cause appearance defects such as orange peel surfaces, particularly in the un-patterned areas of packages.
EA-N6008 and EA-N5618 systems incorporate new technology that enables their use for stand up pouches and zipper bags and that increases their usability due to greater design freedom (Figure 3).
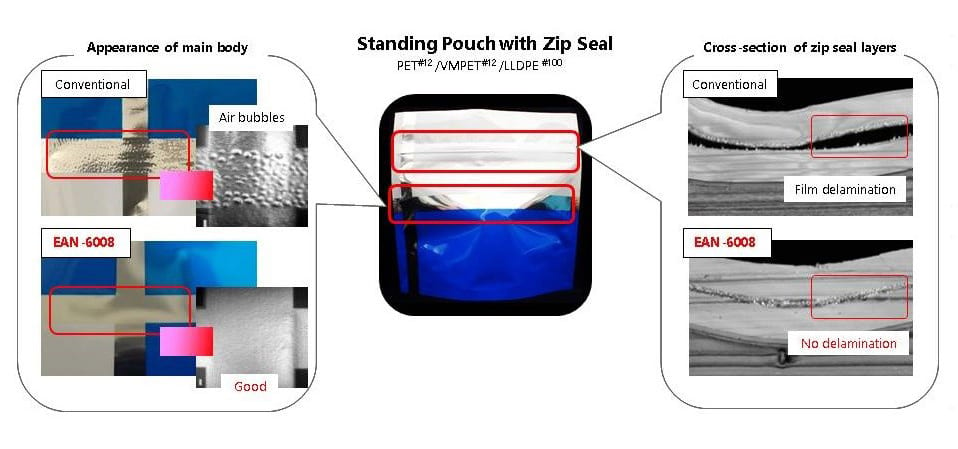
Figure 3. Features of EA-N6008/EA-N5618 for standing pouch applications.
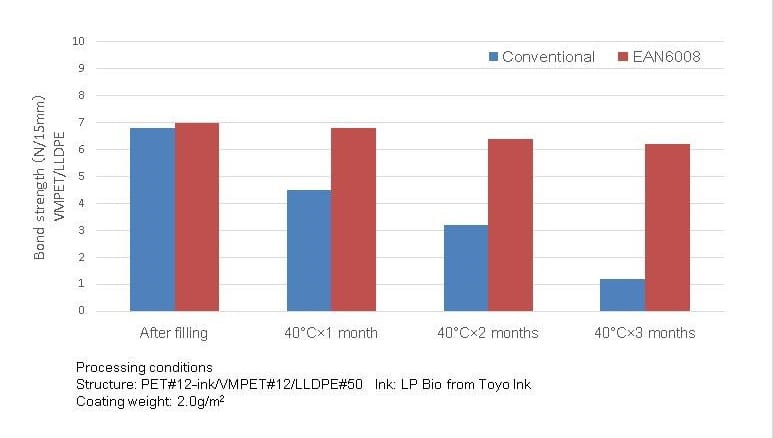
Figure 4. Chemical resistance (hair conditioner pouch).
Furthermore, these systems not only exhibit the content resistance required for refill pouches, but compared to conventional adhesives, they also help to maintain their bonding strength in packages meant for non-food products such as shampoo and conditioner (Figure 4).
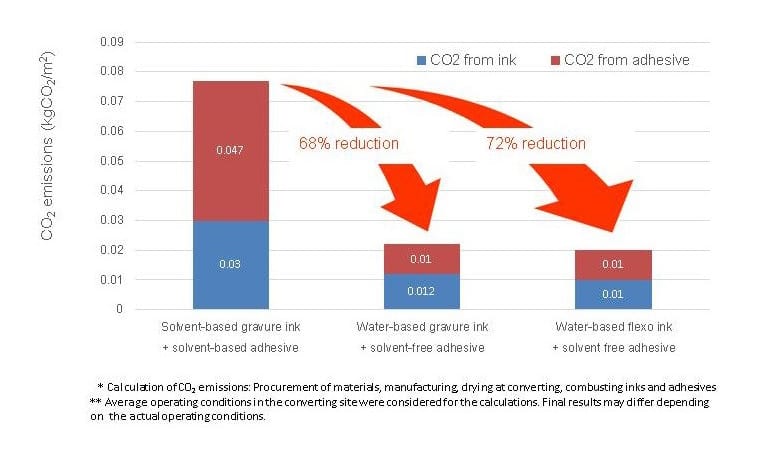
Figure 5. CO2 emissions comparison.
Solvent-Free Adhesive + Water-Based Ink for Transparent Retort Pouches
As mentioned earlier, CO2 emissions can be significantly reduced by replacing solvent-based adhesives with solvent-free products. Using water-based inks in conjunction with solvent-free adhesives to create flexible packaging laminates can significantly reduce the CO2 emissions directly related to ink and adhesives (Figure 5).
Up until now, the combined use of water-based inks and solvent-free adhesives had not been used for refill or retort packaging, as they require greater content resistance. With EA-N6802 and EA-N5802, however, Toyo-Morton successfully overcame long-standing shortcomings by controlling surface appearance through ink/adhesive interface analysis and by designing polymers capable of minimizing the impact of residual moisture specific to water-based inks during the hot and humid seasons. The laminates are suitable for packaging for refills and retort because of their exceptional heat, acid, and chemical resistance. Characteristically, the products do not contain Primary Aromatic Amines (PAA) for increased chemical safety.
Biomass Adhesive Systems for Multilayer Packaging Configurations
In Japan, there is a growing demand for biomass laminating adhesives in the country’s drive to establish a low-carbon society. The Toyo Ink Group has already brought to market the high-performance LP BIO series of biomass gravure inks, which have been building a track record of proven performance over the years. Building on the company's success in this field, Toyo Ink Group released EA-N373A and EA-N6173, an adhesive system that contains more than 10% biomass content and is compatible with the LP BIO ink series.
The outstanding feature of this adhesive is its compatibility with continuous inline lamination methods for three-layer packaging structures (e.g., OPP//VMPET/LLDPE) — a feat that was not possible in the past with conventional products. The company was able to accomplish this by developing a base polymer with drastically improved curing speeds and a high cohesive force. Table 1 shows the results of inline/continuous lamination tests conducted by Toyo-Morton.
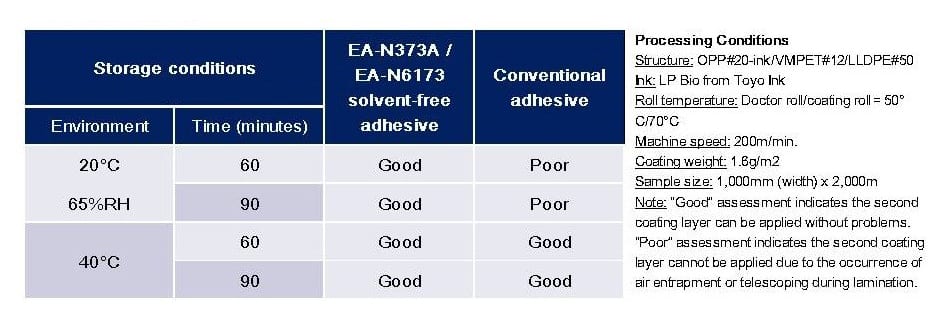
Table 1. Test results.
For the tests, an OPP/VMPET lamination (first process) was winded up to a length of 2000 m. The roll was left at room temperature (20 ℃, 65% R.H.) and 40 ℃ for a specific time. Then, the roll was unrolled again to make the (OPP/VMPET)/LLDPE lamination (second process). Results show that the adhesives are laminatable after being left at room temperature for only 60 minutes. Immediate second lamination is possible, increasing the usability of solvent-free adhesives as a replacement for solvent-based products.
Future Vision
There are still many issues to be solved to further popularize solvent-free lamination adhesives. As a member of the Toyo Ink Group, Toyo-Morton will continue to offer and promote the spread of environmentally friendly packaging materials as the company continues its research and development of solvent-free lamination adhesives. Moreover, Toyo-Morton is continually working to develop products that can help establish a recycling-oriented society. Through these efforts, the company seeks to contribute to the realization of a sustainable society.
Learn more at www.toyomorton.co.jp/en/.
Opening video courtesy of andresr / Creatas Video via Getty Images.