FEATURE
Sustainable Material Pretreatment and Activation Solutions for Adhesives and Sealants
Sustainable Material Pretreatment and Activation Solutions for Adhesives and Sealants
By Mary Battiste, Director of Marketing – North America, Plasmatreat USA Inc.
Plasma technology offers environmentally responsible surface pretreatment while reducing VOC and CO2 emissions.
Sustainable manufacturing is defined as using processes that are environmentally friendly, non-polluting, conserve energy and natural resources, economically sound, and safe for employees, communities, and consumers by the NACFAM (National Council for Advanced Manufacturing — USA).1
Environmentally responsible and energy-saving technologies are more in demand than ever in times of limited resources, rapidly rising energy prices, and the climate crisis. Companies are facing major challenges to minimize their nitrogen oxide and CO2 emissions as well as their energy consumption.
Especially in the field of adhesive bonding and sealing processes, the demand for environmentally responsible production is increasing. Bonding and sealing are highly dependent on the surface properties of the substrate. For example, non-polar polymer materials such as polyolefins are widely used but have poor wettability. Often metal substrates (Al, Cu, etc.) contain surface contaminants that are produced in the material processing stage or are due to handling and storage conditions. In the past, solvent-based bonding agents were the only chemical agents of choice used to treat surfaces. But these solvents contain VOCs and require chemical storage and waste disposal efforts that contribute time and cost to the process.
VOCs occur when solvents and solvent-containing products are used, and they are harmful to the environment. Nevertheless, manufacturing in many industries still involves pre-treating surfaces with primers, bonding agents, or other chemicals that release VOCs. Frequently, more than 80% of VOC-emitting substances used are found in the bonding agent.
In addition to harming the environment, high VOC concentrations also have health effects for those handling the substances. There have been various political efforts to drive forward a reduction in VOC emissions, for example the Paris Agreement for the period 2020–2050, with 195 countries committing to reduce CO2 emissions. Another example is the Chinese government’s introduction, beginning in 2017, of new environmental protection rules, which in 2018 and 2019 led to new requirements for controlling VOC emissions. Because of these and other developments, European and North American companies have become more interested in VOC reduction solutions in their manufacturing facilities in China.
To better comply with sustainable manufacturing practices, some companies are choosing water-based coatings or coating materials with a high solid content in order to meet the requirements of new VOC regulations. But these materials do not bond as easily and require a higher surface energy to ensure proper wettability and bonding for long-term stability.
Surface pretreatment by flame, also used for activation, e.g. for improved bonding processes, is usually carried out with propane or methane gas. As with any combustion of organic substances, this produces a high level of CO2 emissions, which are harmful to the environment. Moreover, products made of polymers that are pretreated by flame could be warped or damaged.
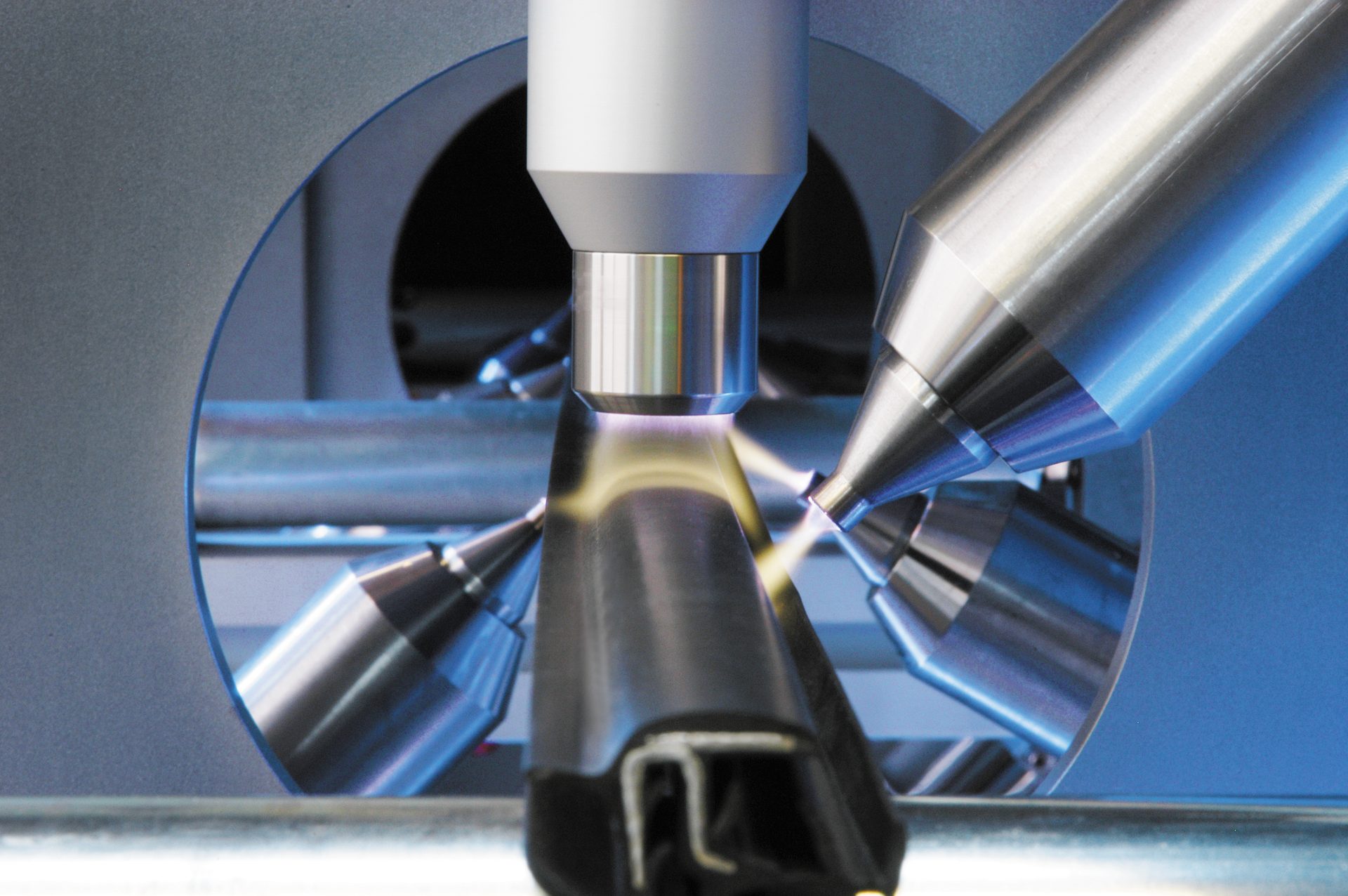
Inline Openair-Plasma® treatment of an EPDM extrusion.
A Better Way
An efficient, reliable and cost-effective alternative is treating the substrate with atmospheric-pressure plasma. Plasma technology is based on a simple physical principle: the addition of energy causes the states of matter to change; solids become liquids and liquids become gases. If additional energy is added to the gas, it ionizes and becomes plasma, the fourth state of matter. If the plasma, with its high energy level, then comes into contact with the material, the surface characteristics, such as polarity, change. Also, surface contaminants (hydrocarbons, for example) are easily volatilized through the reactions with the plasma-reactive species and removed, all in one step. This effect also has a significant impact on different adhesive processes. Whether these involve structural adhesive bonds in cars, electronics protection, or medical devices, these manufacturing processes are possible entirely without liquid chemical waste, thanks to plasma technology and modern, solvent-free adhesives.
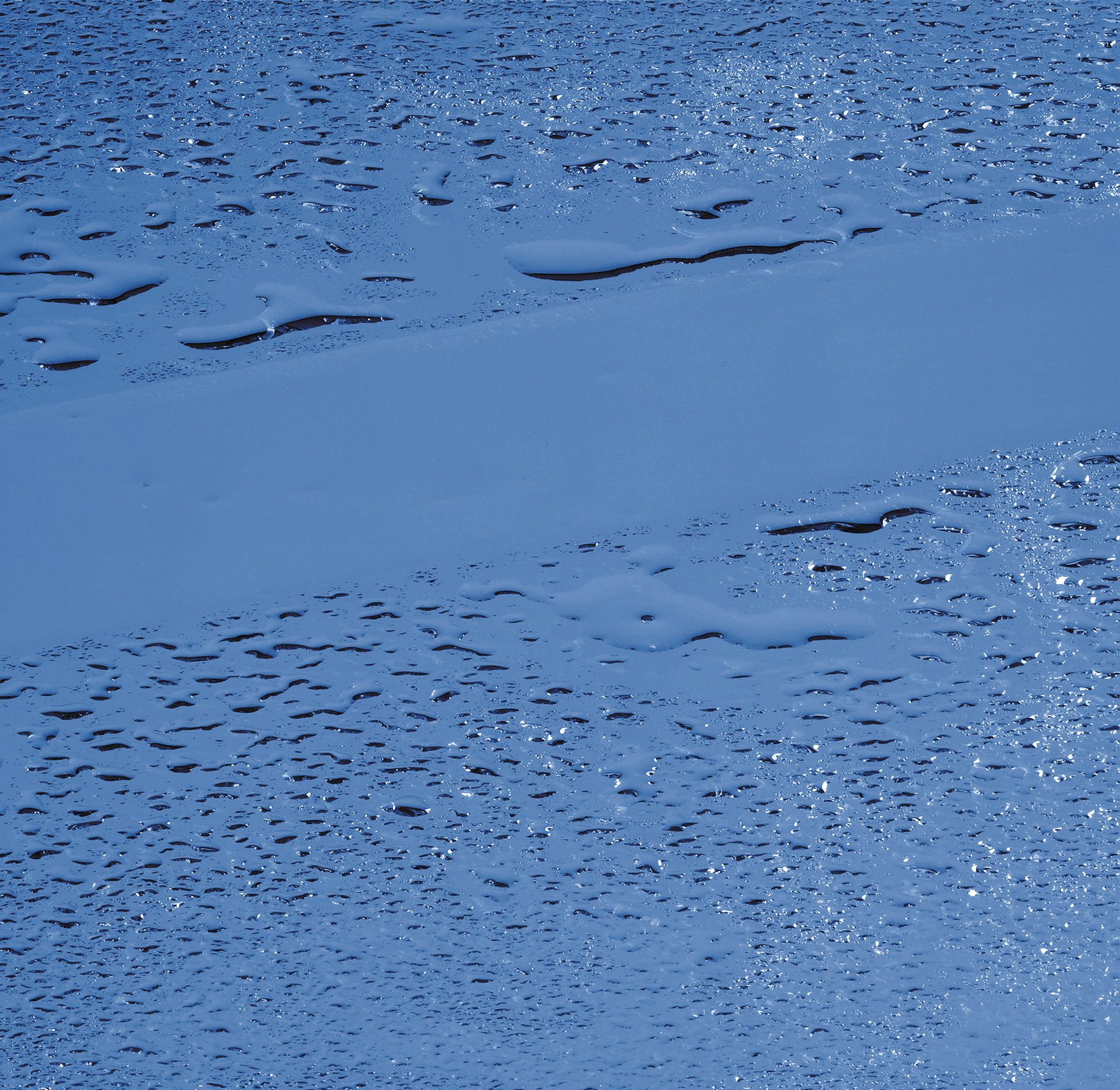
Illustration showing the improved wetting of a substrate after plasma treatment.
This process is dry, non-contact, location specific and fast. Using a comprehensive process-control system, the technology is fully robot-compatible and inline-capable. The production speed is frequently increased by several times, resulting in a reduction in manpower and an increase in productivity.
With plasma, a wide variety of materials can be pretreated simply by selecting the process parameters: from metals that require high plasma intensity with high energies, to a variety of materials that require less energy, to sensitive electronic components that require a treatment free of electrically charged species.
Pretreatment with plasma increases the adhesion and wettability of surfaces, thus enabling the use of more cost-effective material alternatives and new types of material composites while maintaining the quality of the end products.
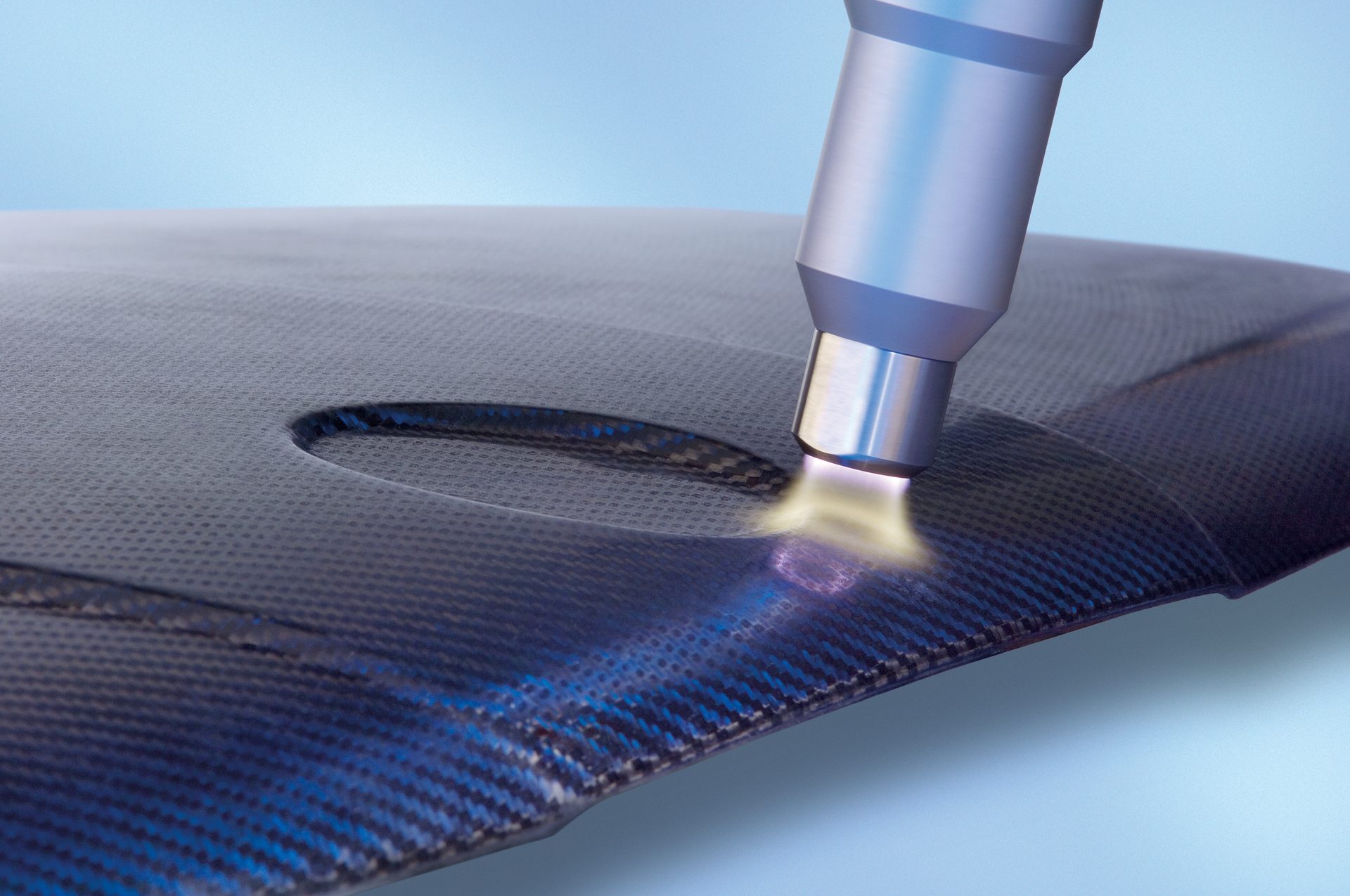
Pretreatment of CFRP hood. The plasma ensures complete, homogenous wettability of the treated surface with paints or adhesives.
Evolution of Plasma Technology
Not all plasma is created equal. The more familiar type is known as low-pressure plasma, where the part to be treated is placed inside a vacuum chamber. This type is a very active plasma with high electron temperature enough to dissociate molecules, but overall, it is only a few degrees Celsius above room temperature. However, this vacuum-based process is not in-line capable, and it can be labor-intensive.
Over 25 years ago, Plasmatreat invented a technology known as Openair-Plasma® (atmospheric pressure plasma). The plasma generation occurs inside a small footprint cavity and is ejected in the form of a jet. The jet design does not require a vacuum pump system, as it operates under atmospheric pressure conditions. The diameter of the plasma plume can be controlled through the adjustment of the jet nozzle tip and can range from a few millimeters to several centimeters. This allows for area-selective pretreatment, so it eliminates the use of masking or large-area application Unlike primers, it can be controlled with pinpoint accuracy and intensity. In addition, it offers inline capability and can easily be automated.
When plasma with its high energy level comes into contact with materials, it changes the surface properties, for example from hydrophobic to hydrophilic. Plasma technology requires only compressed air and electricity for operation. Fine cleaning with Openair-Plasma gently and reliably removes dust, release agents, additives, plasticizers, and hydrocarbons from metal or glass surfaces. Especially with non-polar plastics, plasma treatment achieves surface activation. It supports the increase of surface energy by introducing hydroxyl and other functional groups and thus improves adhesion in subsequent processes such as bonding, printing, painting, and sealing.
Plasmatreat also offers a plasma-based deposition technology called PlasmaPlus® that creates functional surfaces using selective nano coatings on plastic, glass, ceramic, metal, aluminum, textile materials, and more. In this process, the plasma beam is additionally injected with a gaseous precursor tailored to the application, which can be used to produce an ultra-thin plasma layer to achieve the desired surface properties.
These improve the barrier properties, enable long-term stable bonding or coating, serve as a demolding layer in injection molding, provide corrosion protection or effectively support the reliable bonding of hybrid components without affecting the bulk properties of the substrate materials.
Growing raw material prices, increasing quality demands, and the need for more sustainability require new technologies in manufacturing. As a result of the development of plasma technology, surfaces can be pretreated in an environmentally responsible manner, without VOCs or CO2 emissions.
Plasmatreat is an international leader in the development and manufacturing of atmospheric plasma systems for the pretreatment of various material surfaces. Learn more at www.plasmatreat.com.
References:
1. Edited by Paulo Davim, Sustainable Manufacturing (John Wiley & Sons, 2010). https://www.google.com/books/edition/Sustainable_Manufacturing/5y7GLiuOV0wC?hl=en&gbpv=1&pg=PA1981&printsec=frontcover
Article images are provided by Plasmatreat.