FEATURE
PFAS-Free Universal Primer for Low-Surface-Energy Polymers
PFAS-Free Universal Primer for Low-Surface-Energy Polymers
By David Thickens, Marketing Manager, XLYNX Materials, Victoria, Canada
A diazirine-grafted polyamine primer is specifically designed for hard-to-bond, low-surface-energy polymers like polyethylene and polypropylene.
Per- and polyfluoroalkyl substances (PFAS), a large and complex group of synthetic chemicals, have been used in products around the world for more than 60 years. The use of these chemicals in consumer products has become a topic of intense debate, as their prevalence has caused concern among consumers and regulatory bodies. Specialty chemtech company XLYNX Materials, Victoria, Canada, recently launched a new, PFAS-free version of its universal primer called PlastiLynx PXN.
The diazirine-grafted polyamine primer is specifically designed for hard-to-bond, low-surface-energy polymers like polyethylene and polypropylene. Topically applied and cured with either UV light or moderate heat, the universal primer employs diazirine crosslinking technology to form permanent, non-damaging layers of covalent bonds along polymer surfaces that are receptive to all manner of adhesives, dyes, and coatings. The versatility of this diazirine primer also creates new opportunities for dissimilar material bonding and the development of fiber-reinforced polymer composites.
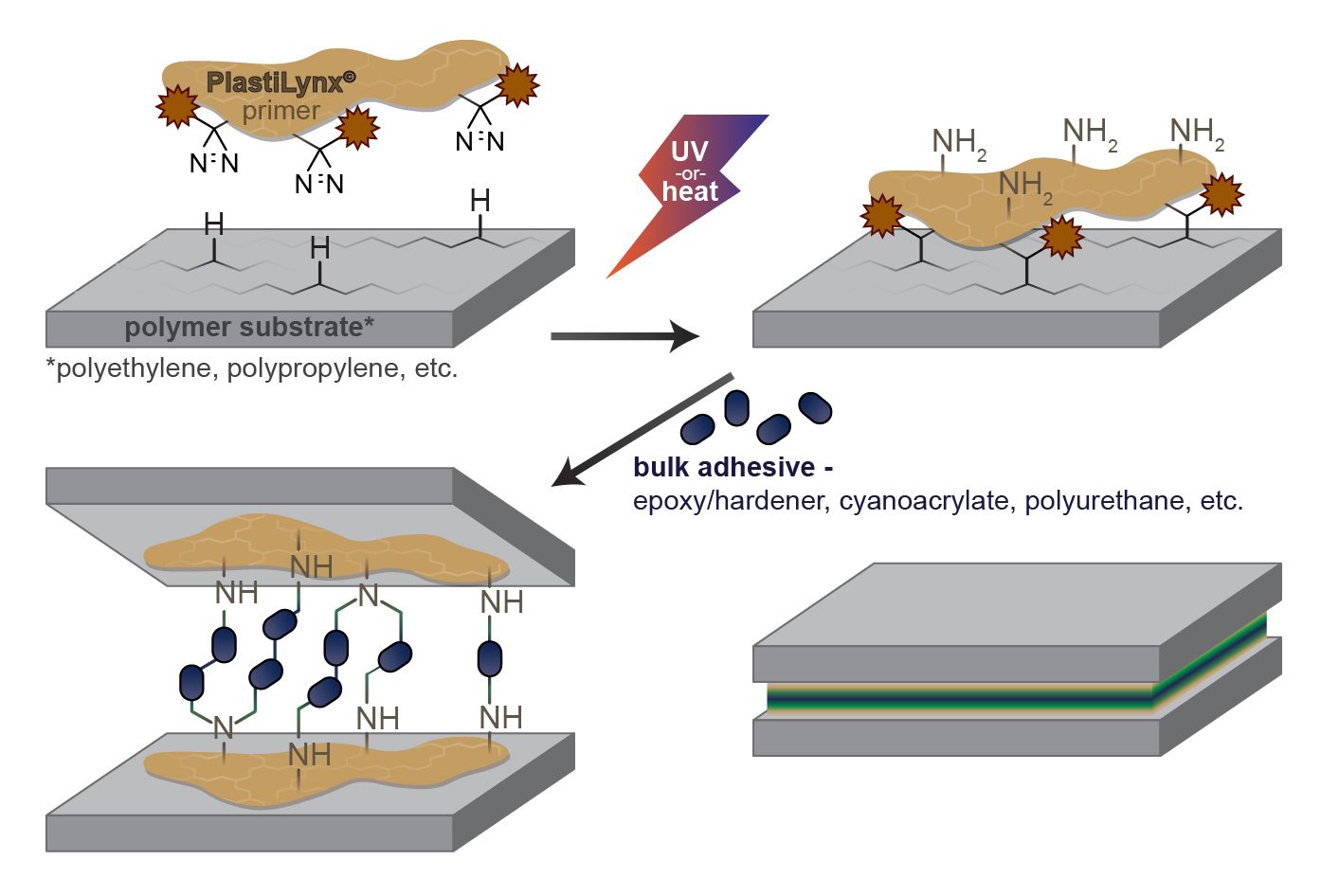
PlastiLynx PXN application diagram.
Diazirine Crosslinking Technology
Diazirines are three-membered rings containing one carbon and two double-bonded nitrogen atoms. When exposed to moderate heat or UV light, diazirines break down, expelling a molecule of nitrogen to form a highly reactive carbene capable of inserting into nearby C-H, O-H, or N-H bonds. Diazirine crosslinking is a technology that has been employed in chemical biology applications for decades, but researchers at XLYNX Materials are pioneering the use of this technology in a materials science context.
Advanced polymers are at the forefront of technological innovation, and low-surface-energy materials like polyethylene and polypropylene are the two most widely produced polymers in the world. Low-surface-energy polymers are highly valued for their lightweight strength, affordability, and durability, but lack the reactive chemical sites to bond well with adhesives, specialty coatings, and dyes. This restricts how these materials can be used, even though low-surface-energy polymers are an integral part of many new and emerging technologies.
Because diazirine technology functions through C-H insertion rather than relying on traditional adhesive surface-energy effects (such as van der Waals forces, dipole-dipole interactions, and mechanical entanglement), the identity of the polymer substrates being treated makes little difference. Strong adhesion can be obtained with various non-polar surfaces like high-density polyethylene (HDPE), ultra-high-molecular-weight polyethylene (UHMWPE), or polypropylene, as well as polar surfaces like poly (methyl methacrylate) or polycarbonate. Bonding polyolefins to dissimilar substrate surfaces like aluminum, steel, rubber, nylon, and glass can also be achieved in this way.
How It Is Applied
The primer is sold as a neat product that must be mixed with solvent to form a solution before use; however, formulation efforts are now underway by the company to develop a pre-mixed solution for greater ease of use. Topically applied by pipette, sprayer, or brush onto the desired polyolefin surface, only a thin layer of the crosslinking technology is required. For reference, the company has found optimal coverage for priming applications can be achieved with a distribution of 0.2 - 2.0 mg/in2 (0.03 - 0.31 mg/cm2).
To initiate bonds along the surface of a treated substrate, diazirine crosslinkers must be activated by curing with moderate heat or UV light. Thermal curing is optimally conducted between 110 °C to 120 °C (230 °F to 250 °F), but higher temperatures can be applied for quicker activation if the melting point of the treated substrate permits. Where possible, the company recommends photocuring with long-wave ultraviolet irradiation (365nm wavelength) for fast activation. UV curing also avoids the risk of damaging a treated substrate with heat. Depending on the intensity of UV light used, photocuring can be completed in a matter of seconds. Once cured, permanent covalent bonds are formed across the surface of hard-to-bond polyolefins, leaving a reactive amine layer that functionalizes the material for adhesive, coating, or dyeing applications (see Figure 1).
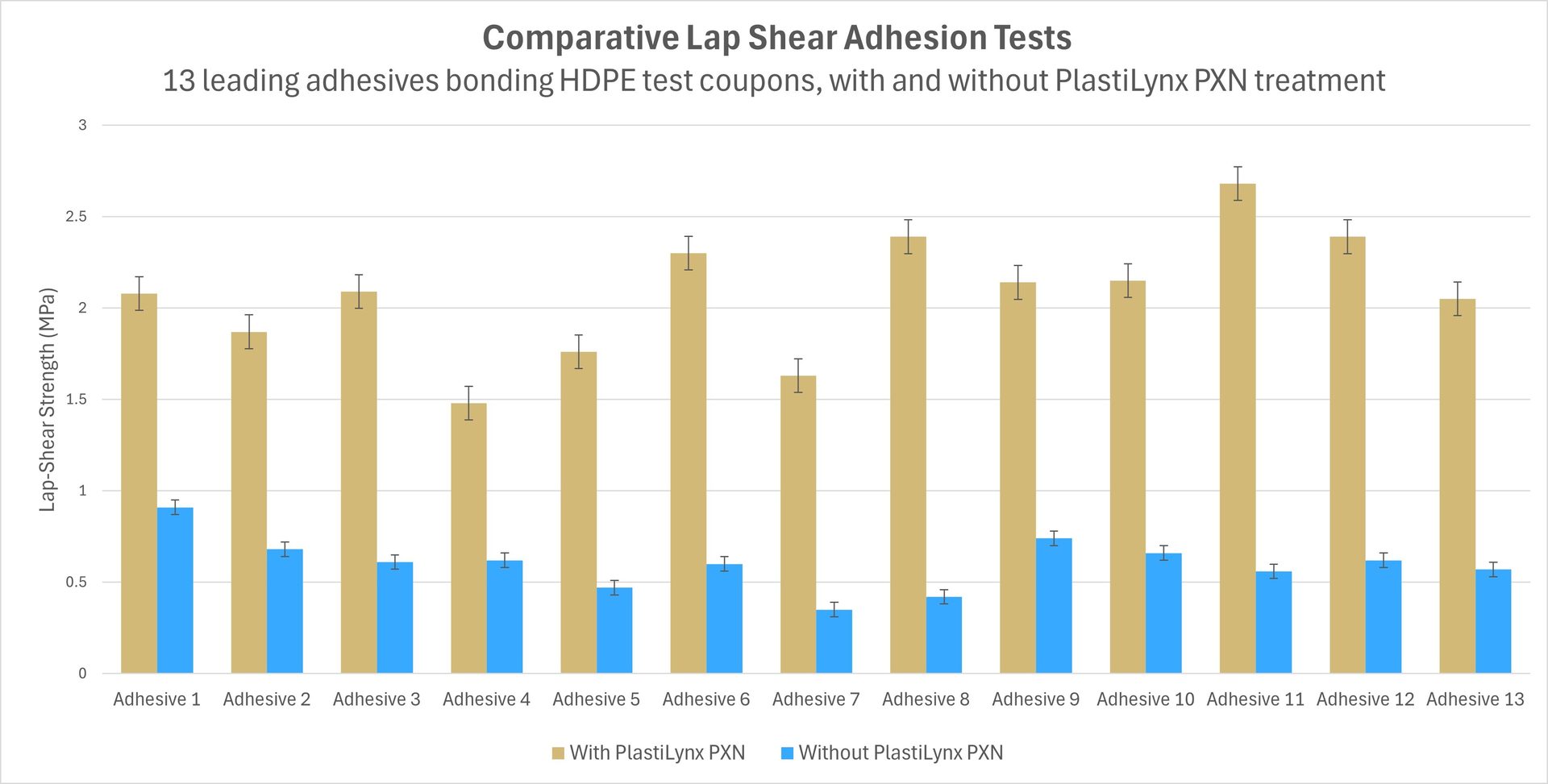
Comparative lap shear adhesion tests.
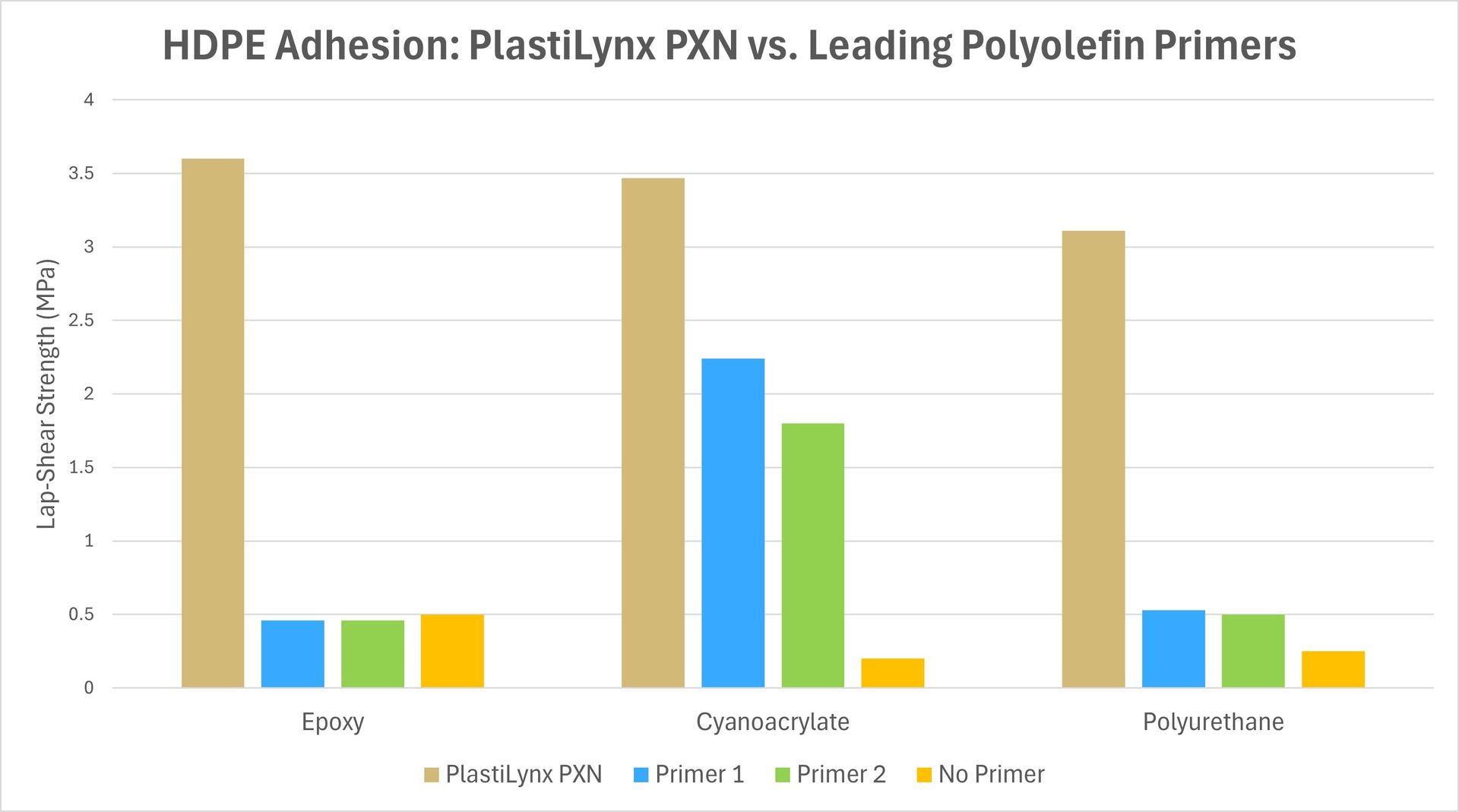
HDPE adhesion PlastiLynx PXN vs leading primers with different adhesive types.
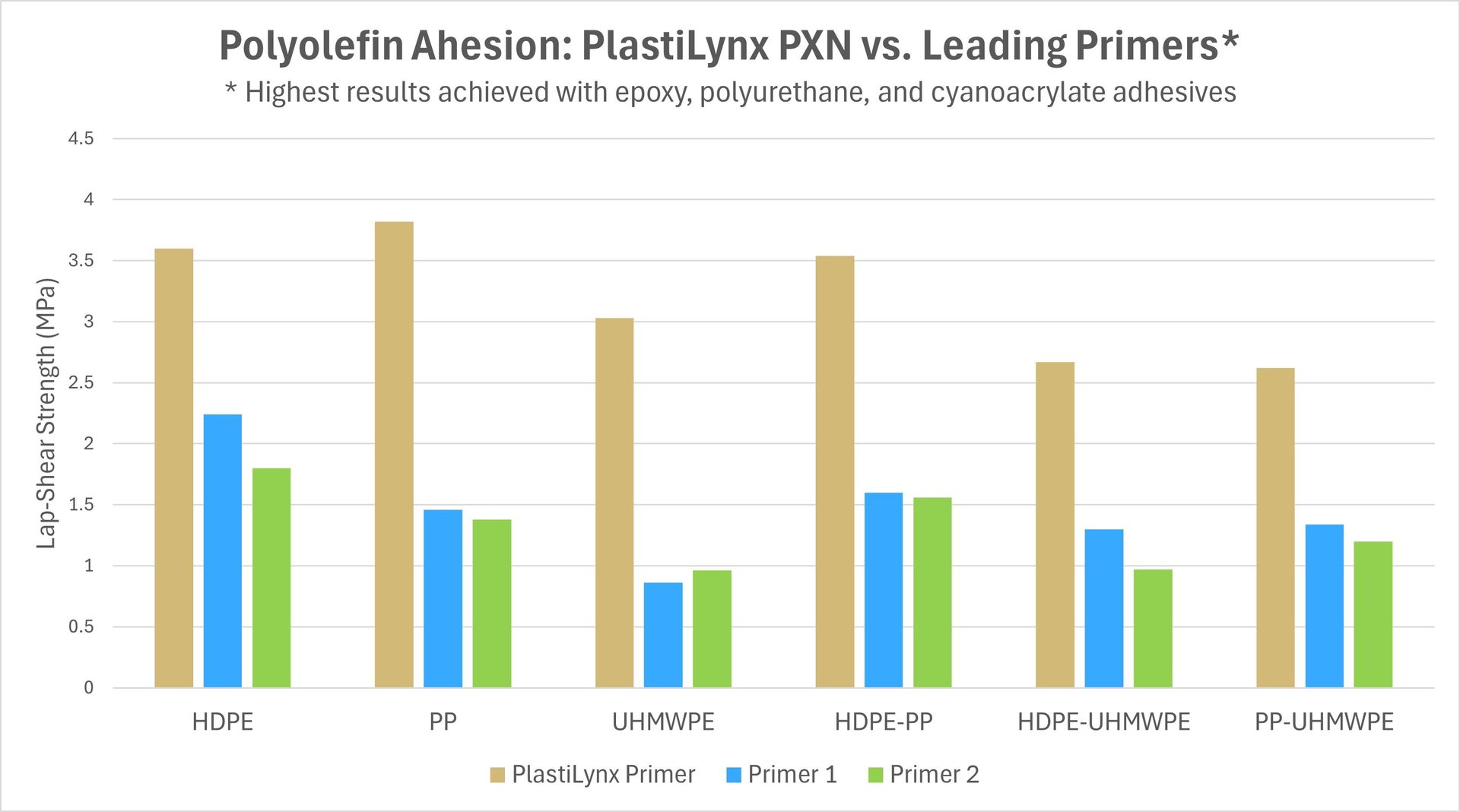
Head to head PlastiLynx PXN vs leading primers.
Priming for Adhesion
Used in combination with commodity adhesives (such as cyanoacrylates, polyurethanes, and epoxies), the primer significantly improves the strength of bonds formed with polyolefins like polypropylene and polyethylene. To demonstrate how the diazirine primer compares to conventional polymer bonding alternatives, the company recently conducted a series of lap shear adhesion tests with leading polyolefin primers and adhesives.
Head-to-head against other polyolefin primers, the diazirine primer provided 150% to 350% better adhesion with polypropylene, HDPE, and UHMWPE test coupons (see Figure 2). Unlike conventional primers, which are designed to function with only one kind of adhesive (typically cyanoacrylates), the tested primer is a versatile "universal primer" that reacts with all adhesive types, including epoxies and polyurethanes (see Figure 3). This versatility means a broader range of applications and dissimilar material combinations (including with metals, fabrics, and rubber) are possible with low-surface-energy polymers. By not being limited to a specific adhesive type, this also means that manufacturers can select the adhesive that is best suited to their application based on cost, curing time, or mechanical properties.
The company also performed a series of comparative adhesion tests using a wide range of specialty adhesives, many of which were designed specifically for polyolefin applications, to demonstrate how bonds created by any adhesive can be improved with the diazirine primer surface treatment. In every case, adhesion between HDPE test coupons treated with the company’s diazirine primer was significantly improved — by more than 350%, on average — compared to what was achieved with untreated test coupons (see Figure 4).
Durability of Primed Substrates
One of the biggest advantages of using diazirine crosslinking technology is that it creates covalent bonds that are incredibly strong and durable. Unlike other surface activating techniques like conventional primers or plasma treatments, the bonds formed by the diazirine primer on polyolefin surfaces remain stable for months, even when exposed to environmental factors like moisture, temperature changes, and sunlight. Stability tests for the new diazirine primer are ongoing, but the company reports no significant reduction in performance after three months of initial surface treatment. This means that materials can be pretreated with the diazirine crosslinker days or even months before their intended use, providing opportunities for greater efficiency and flexibility to manufacturers.
Other Applications
As a universal primer, diazirine crosslinking technology functionalizes low-surface-energy polymers to offer new opportunities beyond adhesion. One such application, published in Applied Polymer Materials, demonstrates how an early generation of the company’s diazirine-grafted polyamine was used as a bridge between UHMWPE and epoxy resin to create UHMWPE fiber-reinforced polymer composites. UHMWPE fibers have high tensile strength and low density, making them an ideal candidate as a fiber-reinforcing agent. However, the mismatch between low-surface-energy UHMWPE fibers and high-surface-energy epoxy makes it difficult to prepare UHMPWE-epoxy composites without relying on destructive and expensive surface treatments. While further research is required, the initial conclusions of this paper suggest an inexpensive, non-damaging path forward is possible using the diazirine primer to create UHMWPE-epoxy composite materials.
The new primer’s versatility was further demonstrated in a recent 2024 paper on UHMWPE dyeing applications, also published in Applied Polymer Materials. UHMWPE fibers and textiles, used in the most demanding ballistic, industrial and adventure sport applications because of their high strength-to-weight ratio and wear resistance, are also known to be highly resistant to consistent coloration. This study demonstrated how UHMWPE can be treated with the company’s diazirine primer to make it receptive to dyes with a high degree of color fastness. This means that rolls of UHMWPE fabric, once treated with this diazirine priming technology, can be permanently dyed — and precision color logos or patterns can be added to the weave — without the risk of colors leaching into the environment.
XLYNX Materials is currently working with companies to support a wide range of adhesion, coating, and textile strengthening applications. The company is also engaged in research projects to explore the commercialization potential of antimicrobial, antifouling, flame-resistant, and ice-phobic coatings based around its diazirine crosslinking technology platform. Together with its reformulated PFAS-free molecular crosslinker (BondLynx BXW) released in 2023, XLYNX Materials now offers a full range of PFAS-free polyolefin priming and adhesion products to companies taking determined steps to eliminate polyfluorinated chemicals from their product lines.
To learn more, visit xlynxmaterials.com.
Images courtesy of XLYNX Materials.