Product focus
3D Laser System Rapidly Checks Extremely Small Adhesive Beads
Technology monitors and adjusts the application of adhesives and sealants in the manufacture of various products.
By Dr. John Young, Silicone Functional Additive Technical Manager, Wacker Chemical Corp., Ann Arbor, Michigan
3D Laser System Rapidly Checks Extremely Small Adhesive Beads
Engineers develop technology to monitor and adjust the application of adhesives and sealants used to manufacture automotive, medical, and consumer-electronics products.
3D laser-based, computer-vision systems from Michigan-based Coherix are capable of tracking the application of adhesive beads on extremely small, but critically important assemblies found in cell phones, computers, medical devices, automotive electronic-control modules and a variety of other electronic devices.
The Coherix 3D Mini™ can check adhesive beads as small in width as two human hairs at speeds of 400 up to 1,000 times per second, faster and more effectively than 2D systems currently in use. When teamed with a Coherix adaptive process-control software, the company’s 360-degree laser technology monitors and adjusts the application of adhesives to assure that every part meets specification.
According to a company representative, the 3D Mini will reduce assembly-line operating costs by up to 20%. In a recent beta test, a major manufacturer of electronic-control units estimated an annual savings of up to $160,000 in operating costs with the installation of eight 3D Coherix sensors on just one assembly line.
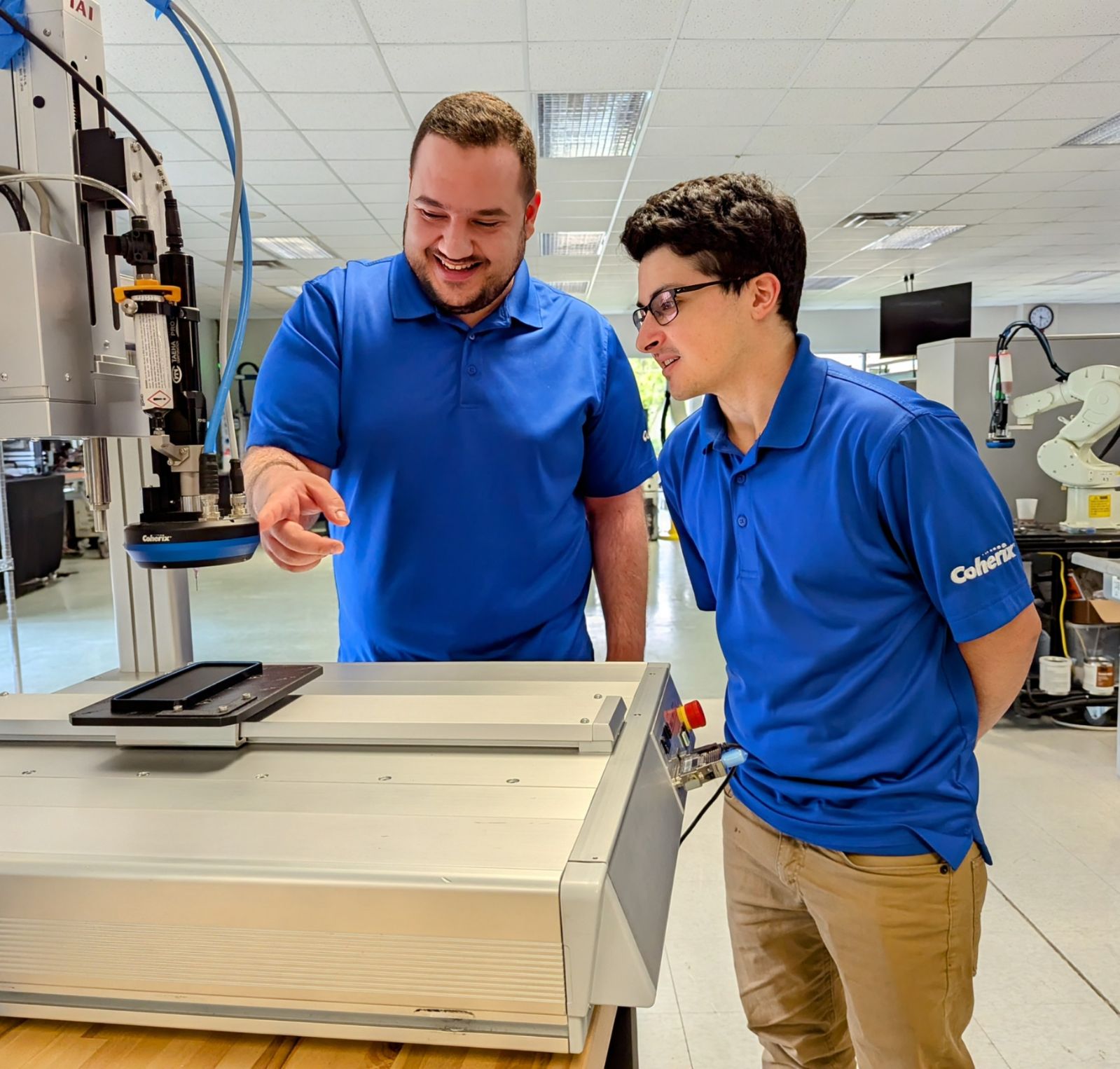
Customer Support Engineers Zaid Herzallah and Julian Rodriguez discuss the new product for auto, medical, and electronic manufacturers.
"Coherix 3D Mini with adaptive process control eliminates the need for additional inspection stations. There also will be a significant increase in production volume along with considerable labor- and material-cost savings," said Coherix President Juergen Dennig.
Less than two days of onsite training is required for assembly-line and quality-control employees to use the new system, and Coherix promises continued support with remote assistance, training, and advice whenever needed.
Production of Coherix 3D Mini already is underway at Coherix facilities in Ann Arbor, Michigan. The company expects annual unit sales to reach 3,000 or more within the next 4-5 years which also will lead to a new North American assembly plant for Coherix products in the relatively near future. Coherix engineers and software programmers spent more than five years on the design, development, and pre-production testing of the new system.
“This is the first laser-based 3D adaptive-process-control system of its kind available for use by the automotive, medical, and electronics industries,” Dennig explains. “It could be years before a truly competitive product emerges.”
Celebrating its 20th anniversary in 2024, Coherix is a pioneer in the development of 3D-enabled adaptive-process-control technology capable of annually saving customers millions of dollars. Coherix APC™ (adaptive process control) software proactively controls the application of adhesives and sealants on assembly lines to prevent defects, increase throughput, and maximize performance.
More information about Coherix is available www.coherix.com.
Article images courtesy of Coherix.