FEATURE
Automotive Innovation: Optimize Your Manufacturing Process with Automated Application of Sealants and Adhesives
Automotive Innovation: Optimize Your Manufacturing Process with Automated Application of Sealants and Adhesives
By Dean Quaderer, Automotive Business Director at L&L Products, Romeo, Michigan
Heat-activated sealants and structural adhesives, combined with automation and robotic application at the assembly plant, can help manufacturers take a bold leap forward in process optimization.
Stamped metal parts have dry-to-the-touch sealant material applied with L&L Products’ XIP® (eXtrude-in-Place™) process.
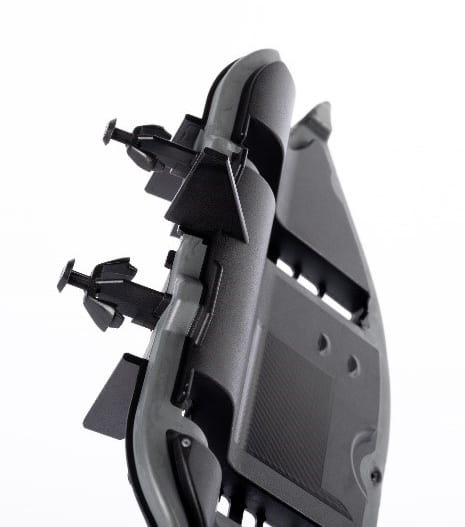
L&L Seal molded baffle with mounting features. Robotic arms can be used to grasp the part and press it in place inside the frame cavity.
Here’s how heat-activated sealants and structural adhesives, combined with automation and robotic application at the assembly plant, can help manufacturers take a bold leap forward in process optimization.
Use the Force of Robotics: Molded Baffles and Composite Body Solutions Reinforcements
Sealants and adhesives can be provided as molded parts for static sealing, bonding, and structural reinforcement. The parts are designed in a wide range of formats and with a variety of material characteristics, including volumetric expansion for gap-jumping and sealing applications. Because these materials are co-molded with a carrier, these dry-to-the-touch parts deliver adhesives or sealants exactly where they are needed. The shape of the parts and the characteristics of the materials are custom-engineered to meet the requirements of specific applications.
Since the early days of the automotive industry, applying adhesives and sealants has been a fundamental and mission-critical aspect of manufacturing. These materials have seen vast improvements over the course of the past century, evolving from animal-based products to modern ambient temperature-cured technologies. New chemistries have enabled process optimization, greater strength and durability, and design flexibility that would be otherwise heavy, expensive, or impractical to achieve.
At the same time, developments in automation and robotics have introduced major opportunities to make production more efficient and less wasteful. Manufacturers can now take advantage of both state-of-the-art chemistries and innovative dispensing and application methods to optimize their production processes like never before.
This evolution of innovative manufacturing technologies alongside innovative materials has made it advantageous for automotive manufacturers to adopt modern methods. For example, a combination of dry-to-the-touch materials and advanced automation technologies have made it possible to apply adhesives and sealants on the assembly line in more efficient ways.
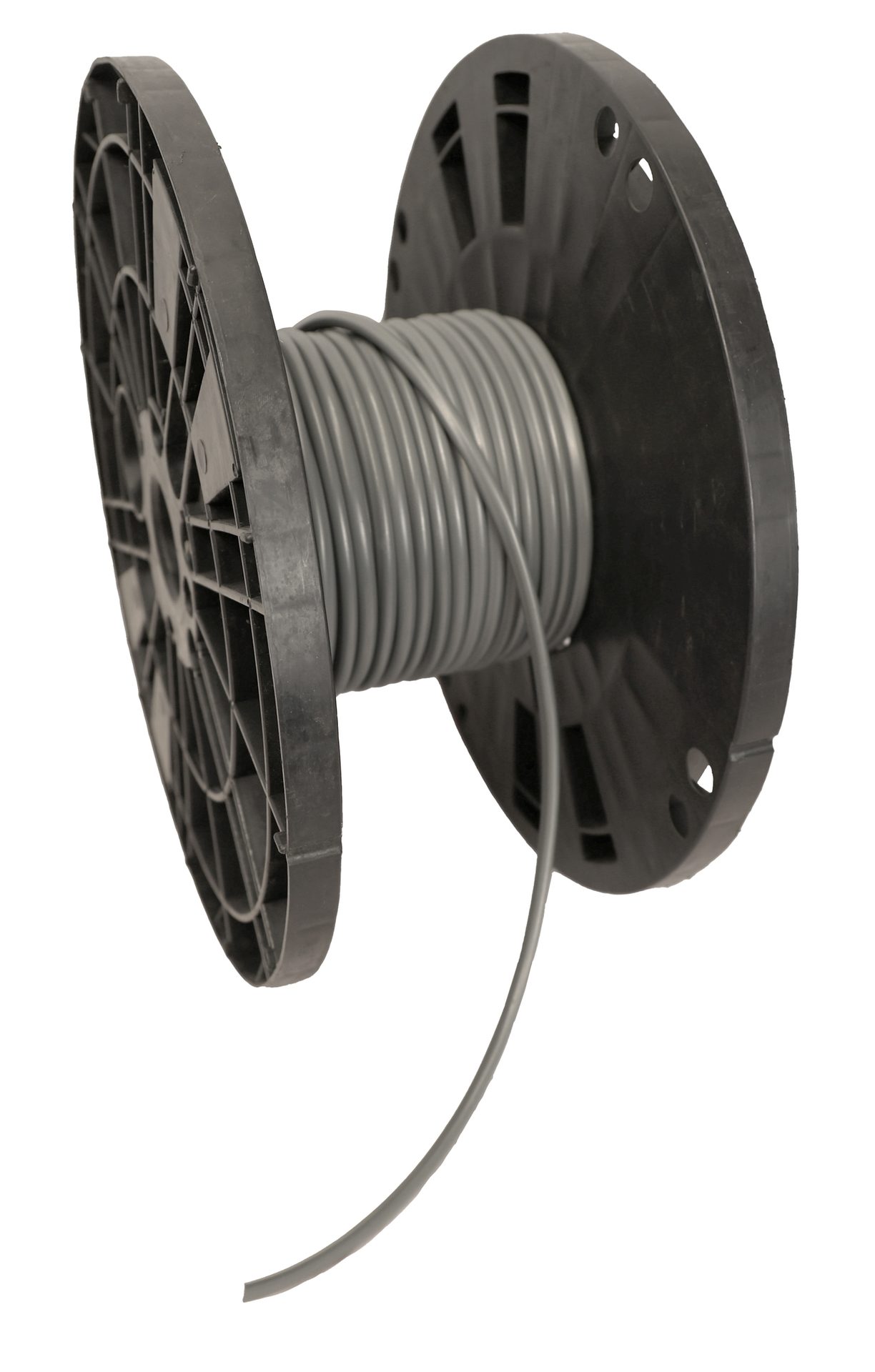
Instead of small tape pieces, the sealant materials could be supplied as ropes or spooled for automated use.
Quality, Consistency, and Savings: Pressure-Sensitive Tapes
Heat-activated materials such as the L&L Bond and L&L Seal product families also provide benefits for manual and robotic application alike. These dry-to-the-touch materials typically come in the form of pressure-sensitive tapes. There are both foaming and nonfoaming versions of these materials, and the material is tuned for specific applications on the vehicle for bonding or sealing.
With the automated installation of the sealant materials on the assembly line, the sealant can be formatted for a more continuous application process with less changeover and downtime. Rather than being provided as small pieces of tape, the sealant materials could be provided in rope form or wound on a spool for automated application. The material can be fed at higher rates for shorter cycle times, and the automated process ensures proper placement and good adhesion to the substrate surfaces.
Ultimately, the combination of heat-activated sealants and robotic application makes the automated process more accurate and faster than traditional application. Well-suited for "lights-out" manufacturing, this helps manufacturers improve product quality and consistency, as well as reduce time and labor costs.
Robotic Repeatability: The XiP (Extrude-in-Place) Process
The faster the cycle time, the more valuable it is to achieve highly precise, efficient, and repeatable results. Applying adhesives and sealants in the automotive manufacturing process certainly fits the bill, as any errors can affect the integrity and safety of the vehicle.
One prime example is the installation of baffles, which are static sealing solutions that are co-molded with nylon carriers and a heat-activated foaming sealant material. While manual installation of baffles requires significant and repeatable force, a robot can be deployed to install the baffles much more effectively and precisely. This automated method delivers the required amount of force for part assembly every time, and parts can be installed around the clock.
Another example is Composite Body Solutions™ (CBS™), an in-cavity structural reinforcement solution for crash durability and NVH (noise, vibration, and harshness) improvement. These dry-to-the-touch molded structural reinforcements consist of a carrier material combined with a foaming structural adhesive. The parts can be located, grasped, positioned, and snapped or welded into place by a robot with the proper amount of force applied to each part.
Once again, the benefits of robotic installation of molded parts make the process faster and more conducive to repeated forceful application. These benefits come back to manufacturers in terms of worker safety, time and labor costs, and product quality and consistency.
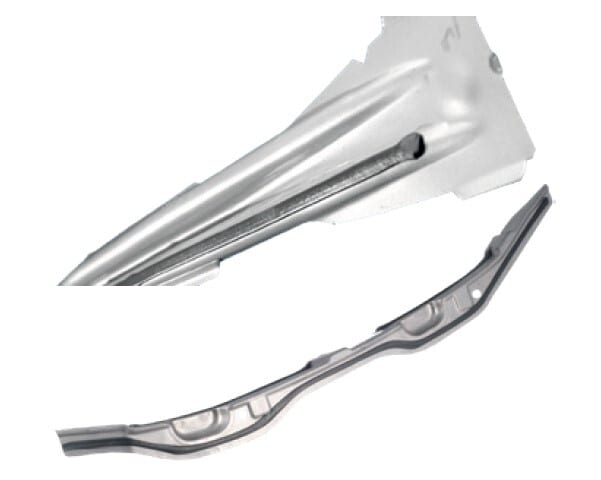
Dry-to-the-touch sealant material applied to stamped metal parts using L&L Products’ XIP® process.
This was the inspiration behind L&L Products' patented XiP® (Extrude-in-Place) technology, which combines unique sealant materials with robotic application. The materials used in the XiP process are designed to be dry-to-the-touch, making them easier to handle and transport after being extruded onto the substrate, whether at a part supplier or on the assembly line.
Just as importantly, XiP provides precise repeatability even for a wide range of applications, including applications in places where preventing water, air, dust, and fumes from seeping into the vehicle is a significant challenge. Compared to manual human application, having a robot dispense these materials directly on the frame during assembly greatly streamlines production precision and efficiency.
The XiP process works seamlessly with heat-activated sealants, and the combination of these materials and the seamless repeatability of XiP can deliver process optimization that results in shorter cycle times and less waste.
Innovative Chemistries and Advanced Automation: Combined Advantages
There is no one-size-fits-all manufacturing application in the automotive industry. However, in the best-case scenarios, the combination of robotic application and state-of-the-art materials can provide several key benefits.
Precision and repeatability of placement: Using automation, the adhesive or sealant material is dispensed in the right amount and in the right place, every time.
Reduction and elimination of waste: In addition to eliminating waste at the point of application, the L&L heat-activated materials are developed to remain firmly in place throughout the E-coat process.
High insertion force eliminates ergonomic stress: For baffles and CBS applications, robots install parts with high insertion force.
Error-proofing: Robots don’t get tired, and they can perform around the clock if need be. They don’t make errors due to fatigue, and because materials are automatically installed the correct way, it eliminates product quality issues related to human error.
Faster cycle times: Large spools of materials, automated forceful application, and continuous 24-7 operation add up to faster production cycles.
Robotic Efficiency with Real Benefits
Through a combination of innovative materials and process optimization, the automated application of sealants and adhesives on the assembly line helps provide benefits to your bottom line and sustainability practices by improving cycle times, reducing errors and waste, and ultimately maximizing efficiencies in your manufacturing process.
At L&L Products, our goal is to help automotive manufacturers optimize their production workflow through our expertise in materials science and production innovation. Let’s talk about how our custom approach to materials science and advanced engineering can help your business succeed in 2025 and beyond.
Learn more about L&L Products at www.llproducts.com.
Images courtesy of L&L Products.