PRODUCT FOCUS
One-Step Cure Adhesive Facilitates Efficient Assembly of ADAS Cameras
Automotive adhesive delivers high precision for active alignment of camera modules, reducing cost, time, and CO₂ emissions.
Lisa Anderson, Founder and President, LMA Consulting Group
One-Step Cure Adhesive Facilitates Efficient Assembly of ADAS Cameras
Automotive adhesive delivers high precision for active alignment of camera modules, reducing cost, time and CO₂ emissions.
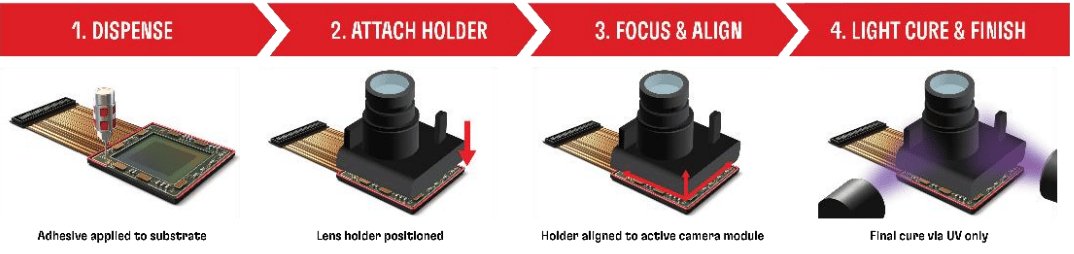
Camera module assembly process with 1-step cure active alignment adhesive reduces process cycle time and energy consumption compared to a regular active alignment process.
The latest innovation in one-step cure adhesives from Henkel is bringing speed, efficiency, and sustainability to the assembly of high-resolution advanced driver-assistance systems (ADAS) camera and lidar modules. Loctite Ablestik NCA 01UV is an active-alignment adhesive that can be cured in a single step with just three seconds of UV LED light exposure. Eliminating the need for oven curing saves time, energy, and CO₂ emissions.
Rodrigo Aguilar, ADAS business development manager at Henkel, explained, “As consumers expect ever more sophisticated assistance systems and increasingly depend on cameras and sensors in the context of autonomous driving, the performance and reliability of these components has become critical to road users’ safety and comfort. As a leading partner to the automotive industry, Henkel is expanding its range of dedicated adhesives for ADAS sensor assembly — providing innovative one-step curing that can meet the performance of preceding generations of adhesives. By enabling active alignment of ADAS sensors to within 100-nanometer accuracy, we are delivering the precision and high sensor reliability needed for vital safety functions.”
The adhesive reaches its full performance and final bond strength with seconds of UV LED irradiation during the fixing step. This means that the time- and energy-intensive post-curing by oven is no longer required. Eliminating the capital expenditure of heat-cure ovens, along with operating and maintenance costs associated with those ovens, makes a compelling commercial case. Additionally, removing ovens from the manufacturing processes frees up manufacturing space.
Henkel reports that with only a few seconds of UV LED cure, the adhesive meets all requirements for high-resolution cameras for automotive applications, while matching its dual-cure predecessors. Offering low and consistent dimensional change of 0.4% during cure, it is a reliable candidate for high-resolution camera modules for automotive as no change in focus from an excessive shrinkage is to be expected. In order to meet the requirements for automotive grade for camera module adhesives, the adhesive shows high reliability and dimensional stability, as well as no outgassing from volatile compounds, ensuring a high image quality and no fogging on the optical system. It is also free of CMT, SVHC, or any toxic substances and fully EU REACH-compliant.
Additionally, the adhesive allows for greater sustainability while enabling higher overall production efficiency. Eliminating the oven curing step decreases the duration of the entire active alignment process, resulting in a more sustainable process that reduces the CO₂ footprint of assembly compared to a regular active alignment process. Henkel reports that the annual energy consumption of a medium-sized oven curing an adhesive at 80° C for 70 minutes (assuming a yearly consumption of about 5,300 kWh) is equivalent to nearly 2.5 tons of CO₂, according to the ecoinvent Database. However, the long-term cumulative effect of eliminating the curing step in a typical production site with multiple ovens will result in a significant positive contribution to sustainability.
Learn more at www.henkel.com.
Article images courtesy of Henkel.