STRATEGIC SOLUTIONS
Trends and Drivers in Adhesives for Wind Turbine Blades
Can adhesive bonding adapt to meet the evolving needs of the global wind energy industry?
By Jean-Luc Guillaume, Director, The ChemQuest Group, Inc.
Trends and Drivers in Adhesives for Wind Turbine Blades
Can adhesive bonding adapt to meet the evolving needs of the global wind energy industry?
The global wind energy industry currently consumes around $600 million of adhesives in the manufacture of turbine blades. Adhesives are used to bond the two shell halves, as well as the shear webs that comprise wind turbine blades (see Figure 1). Adhesives are therefore a key contributor to the structural load-bearing performance of the final wind turbine assembly.
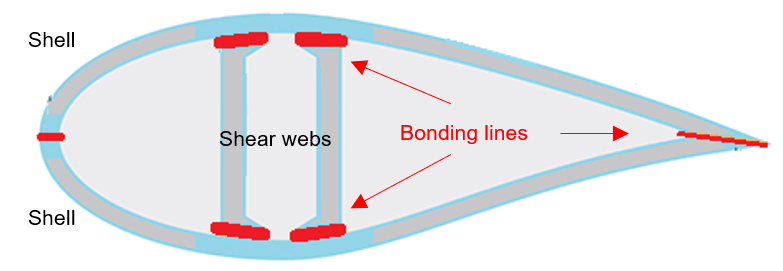
Figure 1. Structural wind blade bonding. (Image courtesy of STRUCTeam.)
More than 80% of the market is served with epoxy thermosetting adhesives bonding epoxy-based blade shells. The rest of the structural bonding market is served with vinyl ester-based adhesives bonding polyester-based blade shells. In addition, some methyl methacrylate-based adhesives are used for nonstructural applications (e.g., shear web pre-positioning) or add-on bonding (e.g., vortex generators).
The market for adhesives in wind applications grows with the wind industry at an average historical CAGR of 5%. Future global growth will rely heavily on continued support from government initiatives and incentives. China represented around 50% of the world market in 2022.
Evolving Bonding Technologies
The current turbine blade bonding technology may be completely reshaped by three opportunities: raw material availability, blade recyclability, and the evolution of blade designs.
Raw Material Availability
It is estimated that the wind industry would need to deliver a CAGR of 15% beginning this year to help meet the global 2050 zero-emission target.1 It is up to the entire wind value chain to step up to deliver this massive growth increase.
Let’s consider epoxies as just one example. The epoxy industry would be required to supply 2-3 times the current annual tonnage of epoxies going into the wind industry. Assuming that the growth rate of other epoxy end markets (e.g., coatings, electronics, and others) continues with an historical CAGR of 4-5%, this massive increase in wind demand for epoxies may exceed the current installed epoxy resins supply capacities by 2025-2026.2
Blade Recyclability
Wind blades are currently the only structural part of a wind turbine that cannot be recycled. While decommissioned blades are mostly landfilled, the wind industry (particularly in Europe) is proactively banning blade landfilling to maintain alignment with the intention of making the world greener.3
Blades can also be shredded and used as fuel for cement kilns. However, cement kilns require an investment to accept “blade waste” fuels.
The wind turbine industry is therefore focusing on the development of composite parts based on a deconstructable resin matrix, enabling the separation of reinforcement fibers and the resin matrix. Both recyclate streams would then be reused in a circular loop to manufacture novel composite parts. Several matrix options — ranging from recyclable epoxy resins to the use of thermoplastic resins — have already progressed to a blade prototyping level.3
Evolution of Blade Designs
Wind turbine power generation efficacy and economics are improving with increasing blade length. For example, a typical industry workhorse blade currently reaches a length of 70-80 m, in contrast to the 35-40 m that was common 15 years ago. These longer blades routinely place today’s average onshore wind power cost below the cost of power generated from fossil fuel.
In the race to longer blades, control of blade quality is key to success. Alternative blade designs and blade manufacturing processes are therefore being developed.
Toward that end, the blade manufacturing industry is likely to move from a full-blade molding process to a pre-manufactured components assembly process, necessitating novel adhesive performance. A good example of this evolution is the emergence of modular blades incorporating modules possibly made from different matrix chemistries, including thermoplastics.4
- Blade recycling — debonding on demand. In an ideal blade recycling loop, the adhesive would deconstruct under the same conditions as the blade shell. However, only a few adhesive developments formulated from the chemistries designed for recyclable blade shells are available.
In addition, these novel adhesives should generate a total cost of ownership equal or ideally lower than the current state of the art while meeting all the health and safety requirements in place around the globe. The adhesive formulations providing the best balance between all these sometime contradictory requirements will win the race.
- Faster cure with workable open time (ideally cure on demand)
- Ability to bond substrates with different chemistries with minimized surface preparation; this would allow blade designers to create blades from pre-manufactured components with multiple chemistries, providing the best component performance for the safest raw material availability and the lowest cost
Next-Generation Adhesive Features
The overlap of these three trends creates a dynamic landscape, opening many interesting opportunities for adhesives formulators. To ensure successful adoption, next-generation wind blade adhesives should ideally provide a series of key features over the current state of the art:
- Blade design — improved mechanical performances to better manage the weight and therefore the bill of material of longer blades
- Blade manufacturing — improved processability to reduce the blade mold occupancy time and minimize production costs
For more information, contact the author at jlguillaume@chemquest.com or visit https://chemquest.com.
References
1. “Global Wind Report 2022,” Global Wind Energy Council, https://gwec.net/global-wind-report-2022/.
2. “Wind Turbine Blade Manufacture,” STRUCTeam Ltd., https://www.structeam-ltd.com/wind-turbine-blade-manufacture-2/.
3. “U.S. and European Views Differ over Disposing Wind Blades in Landfills,” Wind Letters, September 17, 2021, https://www.windletters.com/post/u-s-and-european-views-differ-over-disposing-wind-blades-in-landfills.
4. “GE Awarded DOE Grant to Research 3-D Printing of Wind Turbine Blades,” press release, February 5, 2021, https://www.ge.com/research/newsroom/ge-awarded-doe-grant-research-3-d-printing-wind-turbine-blades.
Opening image courtesy of XtockImages / iStock / Getty Images Plus.